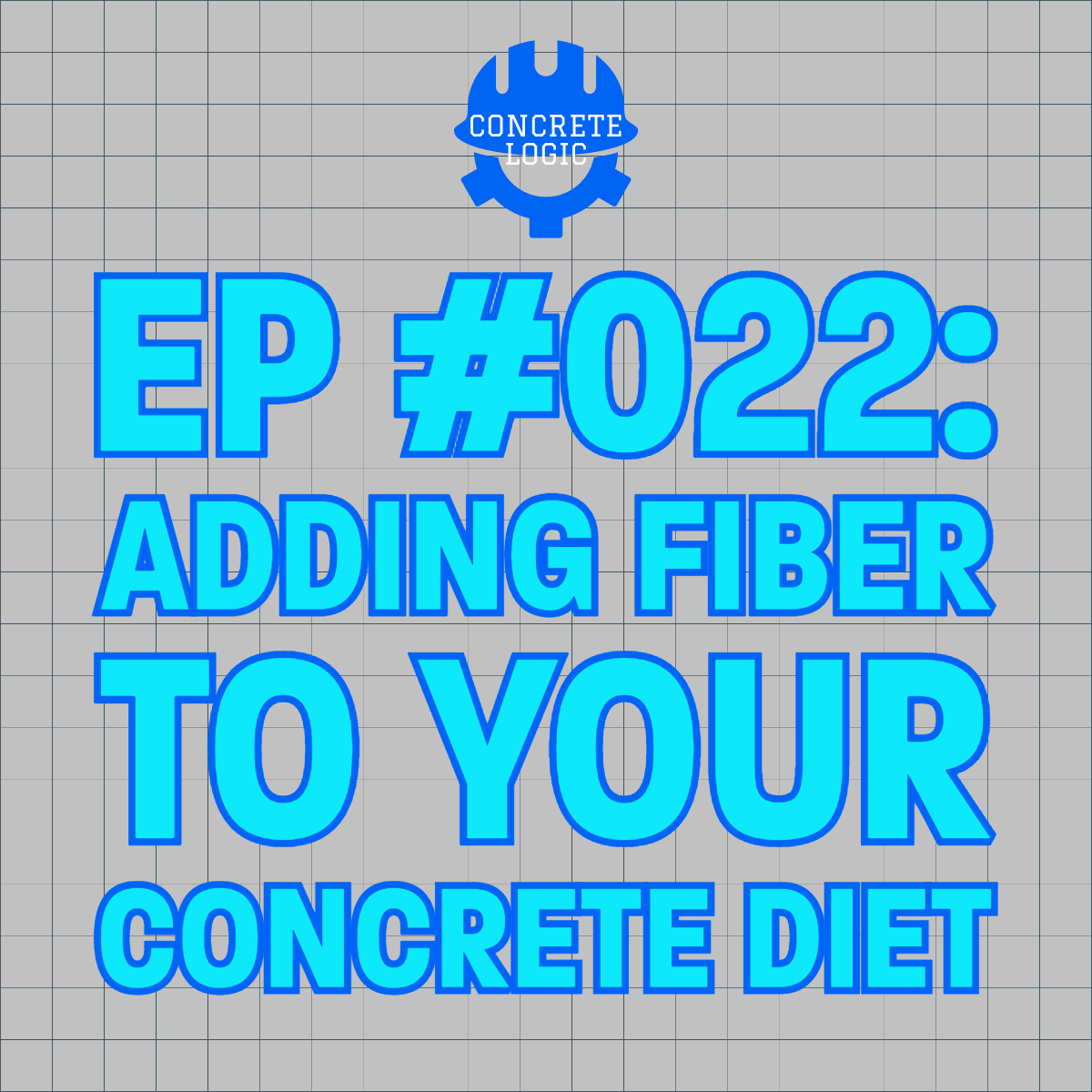
Over the last couple of years, what decades-old technology did the concrete industry routinely turn to when wire mesh became unavailable and too expensive?
Synthetic Fibers.
In this episode of the Concrete Logic Podcast, we sat down with Kristin Crawford, Bill Coursen, and Gerry Welch from Forta Concrete Fiber. Forta is a manufacturer of concrete synthetic fibers. Listen to this episode and find out:
Episode References
Guest: Kristin Crawford | Forta Concrete Fiber | kcrawford@fortacorp.com
Guest Website: https://forta-ferro.com/
Music: Mike Dunton | https://www.mikeduntonmusic.com | mikeduntonmusic@gmail.com | Instagram @Mike_Dunton
Host: Seth Tandett, seth@concretelogicpodcast.com
Host website: concretelogicpodcast.com
Seth: [00:00:00] And welcome to another episode of the Concrete Logic Podcast. And today I have some folks from Forta. Kristin, you want to start us off and tell us a little bit about yourself and then hand the mic over around the table.
Kristin: Today we have Jerry Welch and Bill Corson here with us today.
Bill Corson: I'm Bill. I'm the Vice President of Sales.
Jerry Welch: I'm Jerry Welch. I'm the Director of Engineering Services.
Seth: Yeah, and so I asked Kristin to come on and she brought all the troops with her. So that's awesome. Thank you, Kristin.
Yeah, so obviously Florida is since we got you on the podcast, we're going to talk fibers. [00:01:00] That's what y'all are known for so I was hoping that we could talk about the origin of Florida.
Y'all have been around for what? Since 1978, I think is what I saw. Could you all talk about it? How you got started?
Bill Corson: Sure. I can give you a little bit of overview on Forta here. Back in the late 70s Mr. Roger Lind, the founder of Forta, he was actually at dinner in Pittsburgh and a gentleman at the time had a handful of these fibers.
And he was looking for someone to be a distributor here in the U.S. for them. And Roger got to talking to the gentleman and really kind of was intrigued with this product, these synthetic fibers. So Roger eventually went back over to Switzerland and met [00:02:00] with the company. And really a long story short, he ended up buying the company in Switzerland and bringing the company and all their manufacturing equipment here to Grove City, Pennsylvania.
And started Forta Fibers in 1978 and so really, I mean, fibers have been around here in the States for 40 plus years now. And I mean, I know just a little bit more background. Interesting story. My mentor Dan Biddle he's retired now, but. The very 1st bag of fibers here sold in the States was into precast birdbaths.
Fibers have come a long way since 1978, where selling into precast birdbaths now in the industrial and commercial floors and pavement.
Seth: Yeah, I was going to ask you what the what that company was doing with the fibers way back then. Is that what the Swiss company was doing?
Bill Corson: [00:03:00] Yeah, I mean, the technology came from Europe and was brought over here by Roger Lind to be used in the states.
And now it's 40 plus years. It's, used worldwide in numerous different applications. Like I said, from interior floors, the metal decks, the pavement, the precast.
Seth: And then from there I mean, as far as being mainstream is Forta fibers in general, have they wouldn't do you think they hit mainstream?
Because I, you know, like, I was sharing with you all I've, only been aware of fibers and concrete the last probably 4 or 5 years. And actually use them. When do you all have seen them as far as being more mainstream?
Bill Corson: Yeah, originally the probably the 1st original fibers were microsynthetic fibers and then [00:04:00] really where you start to see fibers take off is when we introduced macrosynthetic fibers to the industry a number of years later.
And that's where you start to see the fibers kind of go mainstream because now, we're getting into the replacement of your heavier wire mesh and rebars, temperature shrinkage reinforcement. So once macro fibers hit the market, that's where we started to see the industry really take off with the use of fibers.
Jerry Welch: So I find it funny that you feel fibers just hit the mainstream recently because actually fiber reinforcement has a longer history than concrete actually fibers go back to as far as Mesopotamia and Egypt. You know, like 1200 B. C. and actually before actually Roman concrete was even invented you know, this is how long ago it is Portland cement was only invented in 1824.
We have actually fibers being used in the Alamo in 1720, [00:05:00] 1718. So fibers go through there from a natural standpoint, and then in the turn of the century, we started using synthetics and glass coming in the 60s. And so where we actually brought this to the U. S. market. And like we said in 1978, currently, you know, from the 2000s on is where we're seeing this macro fiber being used in the industry worldwide.
Seth: Yeah, no, I, now that you say that, now that you say that I see what you're saying as far as it's been around for a long time. But I guess in my world, it hasn't been around a long, time. So we're already spouting out of some terms here. Macro, microfibers. I think this would be a good segue into let's, explain what those are.
So if we could start with microfibers, what are microfibers? And then what are macrofibers?
Jerry Welch: And actually micro, the delineation on fibers is actually under ASTM This is actually the measurement of 12 thousandths of an inch in [00:06:00] diameter. That's the break point. Anything below that is considered a microfiber.
Anything above 12 thousandths of an inch in diameter is a macrofiber.
Bill Corson: Yep. Another explanation would be your microfibers. You really have two types. Micro being a monofilament, short, smooth, round fiber typically half inch, three quarter inch long. They're used for plastic shrinkage reduction.
A typical dosage with these micros might be one pound per cubic yard of concrete.
Jerry Welch: We talk about it being financial hair, millions of pieces per pound.
Bill Corson: And then the other would be your fibrillated fiber. And when we say fibrillated, you can kind of actually open these up like a screen or like a mesh.
When you mix them in the concrete, they open up, give you, they help with plastic shrinkage as well and give you a little bit of hard and concrete benefits. And then when you really get into your macro fibers, The macro [00:07:00] fibers are longer, heavier duty fiber where we're getting into the replacement of your heavier steel, like road mesh and number 3, number 4 bar, that type of thing.
Jerry Welch: I think it kind of gives you some presence of mind. This past year, there was 33M pounds in the domestic market on fibers being used. Roughly, I think we know in the around 30M on micros.
Bill Corson: Yeah, and back up a little bit. I mean, what we're getting into is the replacement of traditional steel reinforcement.
And as you know, Seth, you've been in the field. I mean. Wire mesh and rebar can be difficult to work with. I mean, you have to put it on chairs. And you have to make sure you get it located properly within the cross section of that concrete. We've all seen instances where concrete trucks driving over the mesh and pushing it down to the ground.
So with [00:08:00] fibers, I mean, do you just mix them in the back of the ready-mix truck and your reinforcement is already in the concrete? So it's a lot easier to work with.
Seth: Yeah, so is it 1st, I guess 1st question I got is the micro and the macro fibers, are they made out of the same material?
Jerry Welch: They can be a lot of propylene actually. Synthetics can be anyone from a polyethylene, polypropylene and acetate fiber. So really most fi microfibers are polypropylene or nylon fibers.
A macro fiber is traditionally, sorry. Polypropylene can be steel fiber and can be natural fiber actually not microfibers, but natural fibers for micros.
Bill Corson: I'd say probably 95 percent of the U. S. market utilizes polypropylene. The nice thing with polypropylene is it's chemically inert.
I think it takes 95 percent concentration of hydrochloric acid to start [00:09:00] breaking down polypropylene. And at that point, if you have that much hydrochloric acid on the surface of your concrete, you got bigger things to worry about than the fibers.
Jerry Welch: I think a better way to think about it is the majority of our, the fibers in the market are plastic.
That's really where we're at. Some, derivative of plastic.
Bill Corson:
Seth: And as far as. So with the microfibers, just speaking from my experience, the microfibers would be more of a supplement to I guess your standard reinforcement, your steel mesh and rebar. Is that a correct statement?
Jerry Welch: Yeah, typically micros are only used typically for plastic shrinkage control at the very surface.
We're having some cracking occurring because of either humidity levels paging or high winds causing that the very skin of the concrete to harden crack early so that fiber helps keep that crack together at a micro level. So this is where we're seeing that application [00:10:00] only. And that's the only good only purpose of that fibers is.
It's to work for the first 24 hours of the concrete's life. After that, once the concrete's hardened, that fiber has no other benefit. So we go to the macro, the macros are doing the plastic shrinkage control, but actually have additional benefits in the concrete, such as, again, softness of the concrete, the post crack.
Yeah, that's where we're going to get other benefits going on.
Bill Corson: With the angel hair monofilament, the microfiber we don't recommend replacing wire mesh with that fiber. When we get into the micro fibrillated fiber, we can start looking at replacing a light gauge wire mesh. And then when we get into the heavier steel, that's when we're looking at using macro synthetic fibers.
Seth: Understood. And then so that was interesting. I never thought of the micro [00:11:00] just it being it's use cases for the initial curing of the concrete. I think that might be surprising to some folks at least.
Jerry Welch: Yeah, it goes back to what Bill had said earlier that the monofilaments once, you know, they're smooth and shortened in length.
You know, 1, if the crack were to occur, there's no increment. So there's going to be no post crack capacity. No benefit.
Bill Corson: Yeah, if you think if you visualize a short angel hair monofilament fiber to something like a finish nail, and you take 2 pieces of wood and you tie them together, or you're or you nail that finish nail into the two pieces of wood to anchor them together.
It hides very well, but the problem is, it doesn't really have any way to anchor those two pieces of wood together very well. So it's pretty simple to get those pieces of wood separated. [00:12:00] So if you think about that finished now, like a monofilament, a fine monofilament and then you take that fibrillated fiber.
And picture it as a, like a screw, and you screw those two pieces of wood together, it's a little bit more difficult to get that wood apart because you deformed that material similar to you deformed that steel from a finished nail to a screw.
Seth: Yeah, that's yeah, I, that's a good way to envision that.
The micro it and the microfibers and the macro fibers are there like different types within each 1 of those groups?
Bill Corson: I mean, there's different chemistries really. I mean, like Jerry mentioned, your micro monofilaments are made from nylon polypropylene polyester cellulose fibrillated fibers can only be made from polypropylene. That would be your only choice. You can't take a [00:13:00] fibrillated fiber and have it made from nylon. It's only made from polypropylene.
Jerry Welch: I, think the best description is not all fibers are equal. You know, we have that ability, but a small fiber, small, small length, small numbers gives you a small in diameter.
The micros give millions of pieces going up to the macro fiber. You have different shapes, you have, you know, cross sections, length of fibers, the chemistry of fibers those all add up to give different performances. The modulus elasticity, how rigid or stiff that fiber is, so this all culminates in not every fiber being equal to other fibers.
Seth: Okay, I understand that. I, got a kind of a dumb question. Here's...
Bill Corson: No such thing.
Seth: On this podcast, there is. [00:14:00] On when you're, when fibers are specified, they dosage, there's a dosage in there per cubic yard and it's by pound. So is a, say a five-pound dosage of microfiber and a five pound dosage of a macro fiber.
Is there a difference other than we already talked about once just for the initial curing and the surface cracks preventing those that's the micro and then the macro is more of a structural?
Jerry Welch: It's a good question. Actually, I think keep in mind five pounds of a micro monofilament. Would be like trying to shove a pillow in the back of a concrete mixer, multiple pillowcases with feathers and trying to mix it all up, you know, and then 5 pounds of a macro fiber is like, yeah, we're going to put nails in the back and get this mixed in.
Performance wise you're going to see a big difference because again, you're not going to see a post crack capacity. [00:15:00] With the microfibers, you're going to have mixing challenges with the microfiber, the macrofiber. You should be able to have mixed 5 pounds with no problem. Most fibers and have a good, tough piece of concrete when you're done with it.
Bill Corson: Yeah to that question yeah we, knew for years with the microfibers, if we could get a higher dosage into the concrete, we would get better performance. The problem was trying to get 5, 6, 7 pounds of a angel hair monofilament or fibrillated into that mix and get it to mix properly. And that, that's why well, Jeff Lovett with Forta and others went into research and development to find a fiber that we could get to mix and finish properly. And so with our macro fiber that's what we were able to do was to increase the performance [00:16:00] was introduce our macro fiber that you got very good mixing and very good finishing to try and do both of those mixing and finishing with a microfiber, those types of dosages it would, you'd have a lot of fiber balls and you'd have difficulty getting those fibers to finish properly.
That's kind of really the onset of the introduction of macro fibers because we could get a higher dosage of fibers into the concrete and get better performance.
Jerry Welch: Yeah, I think we're going to see difference between micro macros. I'm going to get increased toughness, ductility, better, more abrasion resistance, permeability, reasonable drop, and small and freezing performance will increase.
Seth: And that's with macro versus fiber. Yeah, macro. So if you wanted to control shrinkage cracks are you saying the macro would, [00:17:00] would do a job as good as the micro or. I mean, how would you address that better?
Jerry Welch: Actually, you framed it correctly. We're controlling the cracks. We're not reducing, but we're going to be controlling the cracking that's going on in this slab at a micro level.
We want to intercept those cracks at the micro level before they become a macro crack. You know, we're using macro fibers to, to attack a micro cracks.
Seth: Okay. So you don't you wouldn't ever have a mixed design where you're had both macro and micro in it?
Jerry Welch: No, you could. By all means you could, because again.
If the conditions of the job are requiring to have a macrofiber, you just want that extra assurance. There's no harm putting in a pound of a microfiber to help you control your plastic shrinkage. Macrofibers you some plastic shrinkage. But really that fiber is intended to be for crack control or toughness.
That's what we're looking for. So we do have clients that [00:18:00] want to see a blended fiber.
Seth: So what would you suggest for best practice if let's say you're doing a slab on grade or slab on ground, where, wherever in the country you're from, you call it different. But if you were to place the typical steel mesh that you see in like a, just a, you know, slab on grade app in a building or office building or garage or whatever. And they want to replace it, would it be best practice to just replace it with macro fibers versus micro or.
Jerry Welch: Yeah, that's what I would recommend is if we have the ideal conditions of a standard job going forward, there's, there was only requirement to use a macro fiber to replace traditional reinforcement.
Bill Corson: I guess really macro fibers can do what micro fibers can do. [00:19:00] Plus, we are doing more with macro fibers like we talked about, because you're using a higher dosage. Macro fibers are typically 3 to 7. 5 pounds per cubic yard, where a microfiber would be 1 to 1.5 pounds per cubic yard. So what the microfibers can do, the macro fibers can do as well, but also increase, like Jerry mentioned earlier, your toughness, your durability.
Your residual strength of the concrete. You're getting a lot better performing fiber with macro fibers.
Seth: Okay. Thank you for straightening that out for me. The we talked about briefly, we mentioned it a couple of times here that macro fibers can replace your traditional reinforcement mesh and rebar.
Is there a, I guess, a limitation to [00:20:00] that? Like what size bar? Could the macros replace, I guess, if you wanted to replace them all?
Jerry Welch: I think it's better to look at not looking at the size of the bar, but more the application. What's the intended use for that steel reinforcement is. If it's for structural purposes, that, we do not recommend doing that.
Again, we're going to give benefit to the concrete itself for post crack capacity. Engineers really need to take that into account when they're doing their design work. But again, if it's a structural in nature. Again, temperature shrinkage all day long, we can be replacing that no matter what size mesh rebar it is.
If that's the intent of what that reinforcement is for, that's what we need to do. A good case in point would be those who know composite metal decks. SDI allows you to use four pounds minimum of a macro fiber for temperature shrinkage control. Yet, the [00:21:00] negative moment that occurs over the beams and girders, you use that rebar.
You can replace that, but it'd be very high dosage because you're putting that rebar into bending. Or mesh whatever, is being used on the composite metal decks. But it doesn't become economical from an overall fiber supply purpose. But again, you want the crack control in the middle of the panels.
That's what the fiber is doing, and you strategically put reinforcement above your negative moment region.
Bill Corson: And we have done a hype hybrid. As well, where the steel, it might be the fields in there for structural, but they'll also include fibers for crack control.
Seth: Yeah, there's a large retailer out there that requires that on all their projects. Yeah, but as far as I'm sorry to beat a dead horse, but [00:22:00] going back to the slab on grade. So I understand what you're saying on the metal decks that there's other forces that happen on a elevated deck like that macro fibers wouldn't be able to replace everything that happens on that.
Jerry Welch: And even it does happen in the slab on ground too. Again if, the slab is a structural slab in nature and the rebar is being used for bending stresses, it's gonna be difficult to re, to equate that to fiber in a dosage. It would just be so high, it wouldn't be a practical solution. But again, we have to work with the engineer of record and understand the design and what's going on functioning with that rebar or mesh.
Seth: All right. And then as far as I was poking around on your website earlier, it. The I guess the main focused in the industry today is being sustainable.[00:23:00] you all have a product out there. It's actually made of it looks like recycled material.
Jerry Welch: Yeah, there is. It's a Ferro-Green.
It is a recycled material. We do make, actually I think more sustainability is just fibers themselves. It's, synthetic fiber is actually more sustainable than the steel reinforcement for today's applications for slab on ground. Most good companies will show you that have EPDs. I'm sure we hear that buzzword in the industry a lot for sustainability.
I need my environmental product declaration to tell you how your greenhouse gases are accumulated. Good companies will have those certificates. To provide to the producers to, to give to the architects and engineers.
Seth: Yeah. Are you all supplying that for your products?
Jerry Welch: We are one of the few that have a EPD available.
Seth: Okay. And [00:24:00] then, yeah, I'm still learning the, I think we're all still learning. What to do with those things.
Jerry Welch: I mean it's, the responsible, the right thing to do. It's out there. EPD comes with a life cycle cost analysis.
So they can account for where all the, your production is coming from and the carbon dioxide carbon monoxide is being produced.
Seth: So is all y'all's products are they? Are they manufactured and Grove City?
Bill Corson: I think it's important to remember. Oh, sorry about that stuff. Go ahead.
Seth: I was asking where your products are manufactured.
Bill Corson: Yep, Gove City, Pennsylvania. And like I said, we ship worldwide.
Seth: I was just asking that because of the that's. You know having something that's locally sourced [00:25:00] manufactured is a I guess a concern. As well.
Jerry Welch: I think that's more on the lead applications for projects with lead certificate certificates and going credits.
Seth: I was saying, I guess, like I was getting at we're, all learning what these EPDs are and how to, utilize them. And but I, think knowing that the product that you're specifying. Even if it's not a LEED credit, if you're still not trying to, even if checking off that box isn't important to you, I think having locally or regionally sourced products on your project would help out as far as your carbon footprint.
Jerry Welch: Certainly. Yeah, definitely. Again, transportation is key in the projects.
Seth: The reason I bring that up is right now [00:26:00] internally, we're just, we're discussing that how to reduce the carbon footprint on the projects that we're a part of. And it might not necessarily be just this piece of paper says. This is you know, this EPD checks all these boxes and it's better than the baseline.
It's also actually to me doing the things that are kind of logical as far as. Things that you can do that are, I guess you can see the result of that effort. Like, if you're shipping things down to the, down from Pennsylvania down to Virginia, that it's obviously you can see, that happening versus, hey, I am shipping the same product from [00:27:00] overseas.
On a ship, a cargo ship and the implications of that as far as your carbon footprint.
Bill Corson: Certainly.
Seth: I don't, I'm just bringing that up because it seems like we get lost in like you all have offered that you all provide these EPDs and I'm not too sure if everybody knows what to do with those things.
I would rather say, Hey, I this, product that you're specifying is we got to import it. It's coming in from overseas. It's going to come in on a ship or you can specify this product that's made, you know, 5 hours up the road.
Jerry Welch: I'll say, I know this part of that. I think where you're getting is the EPD has to be certified by a 3rd party.
And that's what we've actually been able to accomplish is they do take all the information plugged in and validates [00:28:00] the information that was accumulated where it's being manufactured, the transportation costs of it. You can't have an EPD that really you want the EPD that has been independently certified.
Seth: Yeah I'm, skeptical of the whole process. I just think somebody's trying to make some money off of this whole thing. But the good thing about, like you, all have been kind of getting at here is if you use macro fibers and you're able to reduce the amount of rebar reinforcement that's in in a slab or a deck or whatever you're reducing again, the carbon that that, steel would Produce right?
So that's good. But also you're reducing the amount of labor. And if you're reducing the amount of labor in theory [00:29:00] your schedule for your project should be shortened. Definitely. If you're shortening your project, if you're shortening your project. That means you're you someone made this point on a previous podcast, but if shorten your project, that means less equipment out there idling and, burning fuel and all that other stuff that is apparently terrible for the atmosphere.
So I think that's the kind of thinking that we need to have versus Hey, this piece of paper says my product is green. It's awesome.
Jerry Welch: But I think you need down the starting point to be the understanding where you're getting the best benefit from a constructability standpoint.
Seth: Yeah you still got, to build the project, right?
Well but [00:30:00] was there anything else that we didn't hit on as far as what's important? You know, what I was going to ask you what is the what are some of the mistakes that you see folks do as far as utilizing fibers? It could be the application as far as the design. It could be yeah, obviously a concrete contractor, finishing and things like that. What mistakes do you see out there that folks make?
Bill Corson: Yeah, having been in the field for a number of years and seeing a lot of applications go down, I guess, really, you kind of need to start at the beginning. And that's. Yeah. When adding the fibers because with macrosynthetic fibers, you're using 3 to 7.5 pounds per cubic yard.
You got to make sure that the fibers get mixed thoroughly throughout the entire concrete mix in that drum. [00:31:00] So let's just say you're using 5 pounds per cubic yard of a macro fiber. You got to make sure that when you add those fibers at the batch plant that you bring that drum up to mix speed and mix those fibers for roughly 4 to 5 minutes so that the fibers have a chance to get down into the mix, open up and properly break apart and get throughout that entire mix there.
So that's very important. A lot of times I see where the driver might throw it in the drum of the truck and think, okay, I've got a 30 minute drive to the job site. That'll be plenty of time to get the fibers to mix That's really not the case at all. You need to make sure that drum is that mixed beat.
So you get that sharing action to get those fibers dispersed and opened up in the mix and everything. And then the other thing that you run into particularly with a high dosage of fibers is, [00:32:00] let's just say the contractor wants a 5 inch slump. We'll just use that. And you add macro fibers in there at 5 pounds per cubic yard.
It might knock that slump down to a 3 inch slump. What we don't want the contractor doing is adding extra water. That the fibers are only holding that mix together. They're not absorbing any water or anything. It's if you add energy to that mix, it's going to act more like a 5 inch slump when you hit it with energy.
We don't recommend adding extra water to get it back to that 5. If they really do need that 5 inch slump on the ground, then use some type of chemical admixture, whether it be a super P or polycarboxylate, something like that to get it back to that 5. I mean, if you were to pull that fiber out of that mix, it would go back to its 5 inch slump.
It's just the fibers are holding it together. Need to run into that quite a bit. Whenever I've people telling me, well, the fibers are [00:33:00] drying the mix up. It's not drying it up. It's just holding it together because you've got those fibers in there, holding everything up there. When it comes to the mixing or pardon me, the finishing you've seen it, Seth.
Now, not every fiber is created equal like Jerry talked about earlier. There's a number of different macro fibers out there and every manufacturer is going to have their own recommendations. But with ours, I mean, it really has kind of gained a reputation as one of the better mixing and finishing fibers on the market.
When you're using a power trowel, I mean, these fibers do get pushed down into that concrete when you're doing interior work and they hide very well. Really interior work, I mean, I've had contractors who have never used macro fibers first job, and they use 7 pounds and they come afterwards and say that really finished really well. I'll use that again.
Broom finishing for pavement. It is a little bit different. I mean, there's some tips that we [00:34:00] recommend because fibers are three dimensionally dispersed throughout the entire mix. You are going to have fibers on the surface. You just can't get around that. When you're brooming it, I mean, what we recommend.
Is making sure as much as possible, but I know that you can't do it in every situation is brooming in one direction. That way you're laying the fibers down. What happens is when you lay them down in 1 direction. If you pull that broom back across that area you just did, you're going to start pulling the fibers up.
So you're going to start seeing more fibers on the surface. You don't want to get on it while it's still bleeding, so to speak, because the fibers need a chance to anchor in that concrete that keep hold them in there. You also want to angle that broom bristle head down. You don't want to really be pulling at a 90 degree angle across that concrete because it'll start pulling fibers.
You want to Angle those broom bristles down as close to the surface as possible. Clean the broom head as much as possible as [00:35:00] well. I've seen a lot of very good broom surfaces with fibers in them as long as you follow good concrete practices.
Jerry Welch: I think I've seen that from our side, the biggest thing is misuse of fibers.
Someone say, Oh, we need you to add fibers and making sure you want a macro or micro fibers and knowing what does to put in there as some, Oh, just add fibers. And the intent was to add a micro, a macro fiber, but they only added a micro fiber. So that's really one of the bigger things to review a good reference would be go to ACI.
Because it talks about in slab on ground, as well as residential slabs actually fiber design 544 is a good reference to start with, which gives you dosages and performances equated.
Bill Corson: If fibers can be used in numerous applications.[00:36:00] I get questioned on a, lot is decorative concrete being grind and polish. And with our macro fibers, it can definitely be used in those applications for grind and polish. I know I've done the Erie Art Museum in Erie, Pa.
Queens museum up in Queens, New York, and both of those used 7. 5 pounds of macro fiber and done properly. You can get a very good finish on the surface of the concrete. So we all, no matter what the application is, particularly though, with grind and polish, we do recommend first to make a mock-up sure that the owner is satisfied with the depth of the grind and everything.
You know but yeah, so fibers can be used in all kinds of applications.
Seth: Yeah, I didn't know about the polishing. Like I said, I learned [00:37:00] something every, time I do one of these things. I think, there's a good spot for us to stop today. If we want to reach out to you all and, and learn more about Forta and fibers, is it, are we reach out to Kristin or we reach out to all y'all or what's the best way?
Kristin: Yeah, feel free to reach out to me. You can also find Forta on social media, LinkedIn, Facebook, Twitter, make sure to check out our YouTube channel for best practices regarding mixing and finishing as well as project videos.
Seth: All right, well, that sounds good. Thank you all for coming on the podcast today and we'll see you all on the next episode of the Concrete Logic Podcast.
Bill Corson: Thank you very much.[00:38:00]