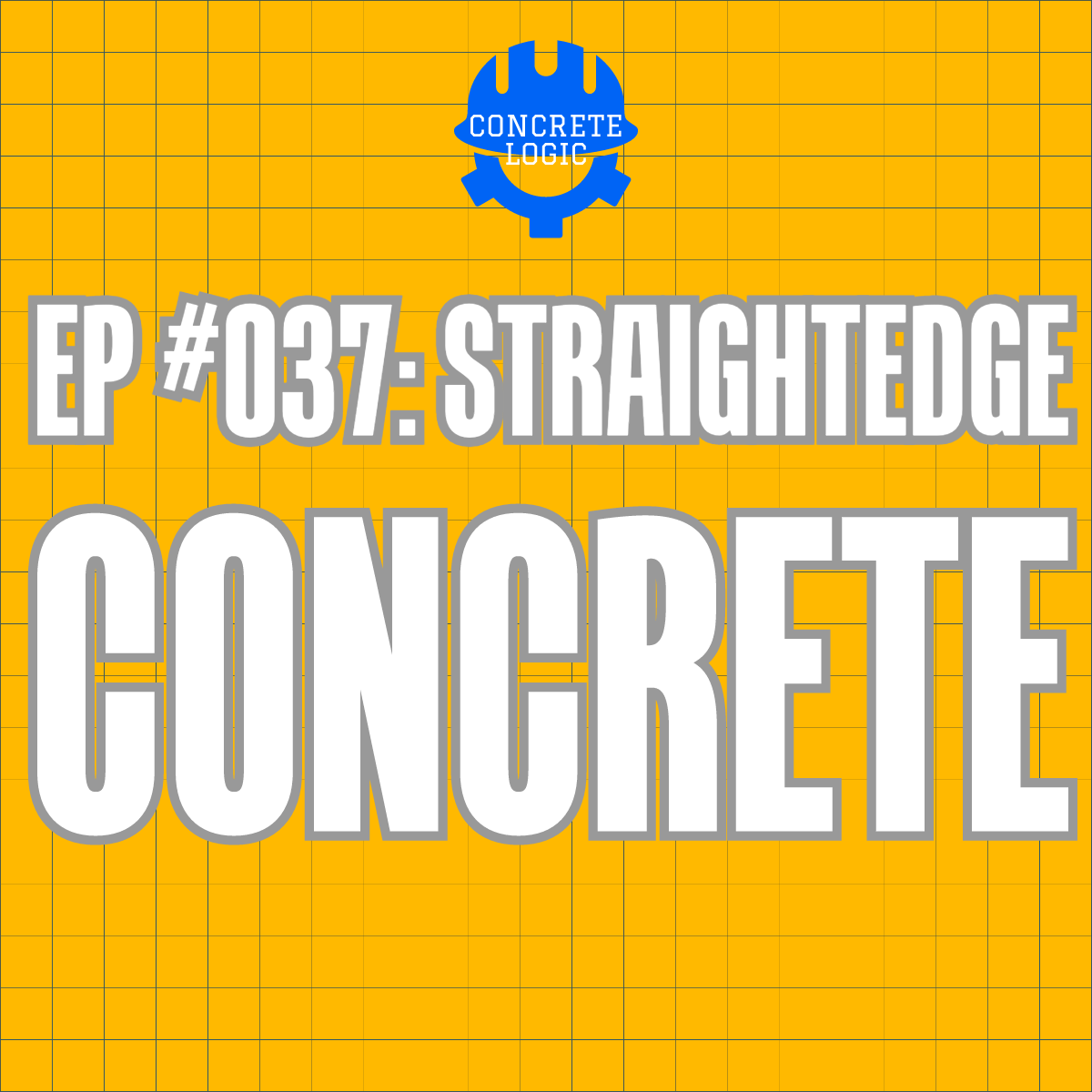
Did you know that Division 9 Floor Covering specifications have concrete floor flatness requirements that don't line up with Division 3 Concrete tolerances?
Does the concrete contractor on your project even know there is a Division 9 specification???
In this podcast episode of Concrete Logic, Keith Robinson of DIALOG joins the show to make us wiser on another concrete industry conundrum - floor flatness.
He suggests a proactive approach to ensure concrete slabs meet or exceed floor installation requirements. Keith points out that even if a concrete slab meets floor flatness requirements days after it's placed, it may not be that flat once the flooring contractor arrives to install floor covering months later.
What can we do to ensure our concrete slabs remain flat? Find out in this episode of Concrete Logic!
Episode References
Guest: Keith Robinson | DIALOG | krobinson@dialogdesign.ca
Guest Website: | https://dialogdesign.ca/
Links to Straightedge Measurement Best Practices:
Music: Mike Dunton | https://www.mikeduntonmusic.com| mikeduntonmusic@gmail.com| Instagram @Mike_Dunton
Host: Seth Tandett, seth@concretelogicpodcast.com
Host website: concretelogicpodcast.com
Seth: And welcome to another episode of the Concrete Logic Podcast, and today I have Keith Robinson with me. Keith, can you tell us a little bit about yourself?
Keith: Sure. I'm a specifications writer, one of the few actual specifications writers compared to the thousands of people. Edit specs for All those I pity, pity the pool of concrete finishers that have to read the documents because sometimes the documents aren't as well informed as they should be.
But yeah, I've been writing specs for 40 years. I create master documents. I write for large clients and basically look after an entire specification team at the architectural company I work for.
Seth: Yeah, and I think you might be the first Canadian I've had on the podcast.
Keith: We're a rare breed,
Seth: yeah, no, we've had some people that are close to Canada. I tease my wife, she's from Michigan. I tell her that's like little Canada, cuz I used to I used to go up to Windsor, Canada on, I'm on this side of the country. I know you're on the other side, but always thought Michigan was kind of part of [00:01:00] Canada, especially the way they talk.
Keith: So yeah, we do too. Yeah, we like guys from Michigan.
Seth: Anyhow yeah. So, Keith thank you for coming on. Your I guess my timing or your timing couldn't have been better cuz the last podcast we released was about flooring adhesive. And you sent me a white paper that you wrote that is about floor finishing for concrete as far as flatness.
So I, was like, oh man, this is uncanny timing. Or Keith's Keith knew when they reach out to me, but so could you tell us a little bit about this white paper, and then I'll ask some questions as you go along.
Keith: Sure. I, I work, I do work for a number of trade associations in Canada to try and align their work practice with specifications.
And for several years now, I've been working with the National Floor Covering Association of Canada. They've had issues with floor flatness, literally for decades, and trying to establish. Responsibilities for the concrete trade, responsibilities for repair and finishing, and preparation of floor services ready for installation of resilient floor coverings, carpets, hardwood, you name it.
And it seems that it was always a battleground. Nobody accounts for a portion of the work that's actually required to create. A suitable, I'll call it plenary like that aspect of flatness, that doesn't depend on whether the floor is sloped or, whatever. It's the actual gross surface profile of the floor.
And we have standards of the concrete finishers use ASTM E 1155, for the dip meter kind of measurements that's perfect and that's absolutely ideal for looking for the structural tolerances. But it has limitations so far as the application of floor finishes is concerned because it's measured only on certain lines, either, and along a certain length.
It doesn't measure to within the perimeter, it doesn't measure across joints. There's a lot of issues for the floor covering person that doesn't address corrections that need to be made. In order to have flatness that will actually accept, materials.
Seth: Yeah. And what's the dip meter?
Can you explain that to our listeners?
Keith: Oh, the dip meter? Yeah. It's it was an instrument that was invented by, I've gotta get it wrong Face Consultants. And it's a really cool machine. Basically, you run it across the floor, tiptoeing it back and forth across, along either a 45 degrees section across.
A floor area between structural components. And then what it does is it looks at all the waves and it, surface topography. Yeah, that's, yeah. Created by the finishers. They put the trial across, and they, as if you've got a power trial, if you're one, we're under direction, we end up with troughs and furrows.
If they go 90 degrees. If the concrete is not set up in time you tend to get. I call the moguls, like on a scope ski hill. Sometimes very rarely we get the opportunity to go 45 degrees back across that and get really good floors, but, so much of it is the quality of the, that flatness is all about, the concrete going into the project and what the cure time is
Seth: Yeah.
Of the setup time. Yeah. So yeah, there's always. There, there always is conflict with figuring out what the floor flatness is cuz some concrete guys like ourselves, we do that meter the floor flatness. We do that work before the third party comes. And we turned that over to our client ahead of time and say, Hey, this is what we come up with because we're uneasy when it comes to a third party guy and who they send out as far as doing the measurement as well.
So, we try to be in, in front of it that way. And, and it only works if you're being honest with it. So, I'm sure what you've seen is there's ways to different, you can take different lines on that floor and have fantastic results, and then, You can go to another part of that floor and have terrible results.
Meaning, that you're not meeting the floor flatness that is required in the specifications.
Keith: Yeah. And that's allowed in the test methodology, you're allowed a 70% deviation. And it's that's the difference between having, a hole in the floor or a mountain in the middle of the floor.
Seth: Yeah. Yeah. But the. As a concrete guy our concern is staying away from the conduits that come out the floor, the columns and things like that. Because when you're trying to finish around those things it's more difficult. It takes more effort to do that. And so that's I think that's the reason why we, sometimes you take advantage of the, of those ways that you can take those measurements to stay away from those things.
Keith: And I think it's all fair. And I think when you're working with, I mean face it, concrete is liquid stone. It's gonna do what it's want, wants to do. And you're trying to get as close to. A reasonable finish as you can. You gotta spend some time with it. If you don't spend the time, then you get a really horrible job.
Or you spend a bit more time and you get an all-right job. Let's not take away the skill level of good concrete finishers because it's hard work. I did that for one summer. I know what it's like pushing around concrete and it's hard, heavy work. Yeah.
And that's standard as you said, you can run at 90 degrees to the floor. You can run at 45 degrees across the floor. I, it's not like in the old days with the old style straight edge measurement, set up on a level and, randomly placing it somewhere on the floor, you could really cheat that test.
But the, I think the current E1155 gives a really good. Indicator of what the floor condition is along those lines of measurement. And that's where what we're talking about along the lines of measurement, it doesn't really give you an idea of what the floor's like all over.
And I think that's appropriate. Again, the measurement is made within three days of concrete placement. Concrete, as it sets up, it's absorbing water. You've got the sun shining on it. If there's not proper shading, if you've got a low water mix it's, it starts to already start to curl.
You start to get that, the edge is pulling up. And of course, as a curls, it also wrinkles up in the middle like a shrinking apple kind of thing. There's a lot of things that happen with concrete after three days as well. The curing regime that's set up by the, by either, the concrete finisher or the general contractor up here in Canada, it's usually the general contractor looks after the curing.
Oh, wow. And they, we're dealing with freezing conditions and, horrible things for concrete, but,
Seth: So what so what do you normally see up there? What that's different from down here? As far as the general contractor curing the concrete what do they normally cure?
Keith: What they're gonna do is they're gonna go for the highest earliest strength gain concrete mix they can find. They're gonna try to attempt to wet cure it for. Maybe two days if we're lucky. They'll try to, keep it covered for as long as possible, but you gotta keep the building moving.
There's a lot of things for weather that, really don't help that surface condition of concrete as the building ages and of course temporary heat, it's a whole lot cheaper not to heat a construction site than it is to put up plastic yeast and try to heat. Not just that enclosed area, but because those sheets they leak like crazy, all the rest of the outdoors as well.
So also not very sustainable. So there's a lot of things that happened to concrete and that's what the National Floor Covering Association was trying to address that there's more to flatness. Than just that, that I'll call it the wet finishing. You're dealing with plastic, concrete and pushing it around.
And by the time then the floor cover the floor, they call it, the floor covering installer comes on site. Could be six months, eight months. That slab could have been cold for five or six months. Which of course traps any moisture in the slab, so then all of a sudden you throw heat on the slab.
And you get this poof all the moisture that gets driven out of the slab. The slab is cold. You get condensation on the surface. It's just horrible, and it's I don't know what you're talking about. It's 28 days. It's concrete strength is fine, but we tend to ignore the fact that, yeah, no, there's other factors that affect the quality of that concrete slab.
All of which actually changes over time. It probably settles down after about nine months to a year. The most amount of change on the surface of that slab. So you could actually lose up to 50% of that flatness and levelness that the concrete finisher worked so hard to achieve. So on the day that you measure it, you could get a really, say we got a really flat floor, using, using conventional methods.
You go, FF 30, that's an amazing floor and that'll probably do for almost anything you want to apply to it. But after, six months of those kind of curing conditions, you might be lucky to have an FF 15.
At FF 50, I don't think there's, I don't think there's a concrete finisher alive that would accept that as representative of their work. And it's not what they worked so hard to achieve. No. So there was, there's always this differential coming up and we have clients that I work for that say, I want dead flat floors. I've got a hospital operating room. I've got laboratories, I've got, a high stack warehouse. You've gotta specify FF 50, FF 100. And I'm like, oh, how are we gonna get that and maintain that? And I think most specifiers, they don't understand what it takes, so we just.
And I'll say, we're a guilty party to all of this because we'll just say, oh yeah, we want a super flat floor. Let's put in a requirement for FF 50. Sound like we know what we're talking about. No. It just doesn't work that way because of course the higher you get on your FF the greater that percentage change is going to be over the months.
So, by the time you get to FF 100, which is - special concrete mix, special equipment for placing, special finishing, long-term curing, permanent heat on within, on top of that concrete slab. You name it. It still results in upwards of 70% of that flatness being retained after six to nine months, which is why of course, have a lot of people putting there, yeah, I wanna put in that shrinkage, compensating admixture.
Yeah. It's that only delays the problem. It doesn't actually solve the problem. Yeah. If you don't look after all the rest of this stuff. So we figured out that there's something else that needs to be done, cuz currently what happens is that flooring installer is being made responsible to prepare the cause.
It's floor preparation to fix all of this new topography that happens on the floor. That happened after the concrete was actually accepted that three-day measurement mark. Flooring installers don't have the equipment. They, it hasn't been included in the price. They're being made to pay for stuff that they have no control over.
Right? GC has control over the condition of the floor; up from the time that the concrete finisher leaves the site up until the time that the flooring installer comes on site. A lot of things can happen to the slab and. How do you account for that? In the specification? How do you account for that construction budget?
How do you account for that, your bid? It's an issue. It was a huge issue. Yeah.
Seth: Yeah. So how do we solve that? I don't even know the answer.
Keith: Ah, it's, I'll tell you, in Canada we have something called the Red Seal Contractors program. It's a form of standardized apprenticeship for different trades.
And this, there's a Red Seal program for concrete finishers. It talk, and it talks about all the things that concrete finishers can do, from the placing and leveling and curing of concrete, the repair and remediation of concrete surfaces after placement, right?
The, they also look after, application of, resonance coatings and self-leveling toppings and all sorts of other things. It's all built into that particular trade definition. And I was talking to some representatives from Concrete Canada. They're one of the associations that represents floor finishers.
And they said, “Keith, you're missing something entirely. You've got all that wet finishing well looked after. You understand that's good for you. But you're missing a component of the trade. It's never specified. And when the GC goes out and says, okay, we gotta fix the floor, they'll get called.
They go in and they've got grinders,
They’ve got patch and repair materials. They go in and they basically say it's, we call it dry finishing. So, they'll go in with the grinders and they'll do like a skip grind across the floor. Yeah. Knock off all the high points. And it might be only, a 16th or an eighth of an inch, one and a half, maybe two, three millimeters, which doesn't affect the structural quality of the slab.
And then if there's any drastically lower areas, they'll just, use, use a wide trowel and screen it between two high points to flatten everything out.”
And I was like, “Wow! How do I specify that?”
And they said, “A good thing to do is to start off with a cash allowance.”
And I went, “That's brilliant.”
I remember reading in the American Concrete Institute they asked you to say about cording tolerances between all that Division 3 concrete work and all those Division 9 flooring works. And they said Mr. Engineer or Mr. Architect, you really should include a cash allowance to correct those floor surfaces.
Yeah. And it's oh, wow, this been in front of my face for 20 years. There's a standard that affects the installation of resilience sheet floors, ASTM F710, about surface preparation that says, oh yeah, you might have to mechanically prepare those floor surfaces to bring it into a flatness.
Acceptable to the application of floor finishes. That's been, and by the way Dean Kraft, one of your previous speakers, he sits on that committee and we're, and I'm talking to him and he says, oh my God, Keith, I think we've got it all wrong in the standard. He says that's brilliant. So, what do you propose?
I said first off, we've gotta bring back a straight edge measurement. Because the straight edge is the only thing that really can pick up those surface deviations necessary to prevent material runoff. Like when you're try to place rigid square materials on the floor and you've got a hump in the middle of the floor when you can't cut and trim all those piles Yeah.
To make it fit, to fit around those lumps and humps, you just create a bigger problem than what you started with. So there's this, all of a sudden it's like it was implied in the standard, and then it's like nobody followed up on it. It's oh my gosh. There's your solution. And the best way to measure that is a randomly placed straight edge.
If you can imagine taking a straight edge and pushing it around the floor in front of you, basically, and when you find a high point, you go, it goes, the straight edge goes up. It comes back down again. You can actually measure those high-point areas. You can find the same thing with more technical tools like laser scanners and you some guys use string lines and plumb bobs, to lay out a grid across the floor.
But however, it's done, you can get a really good representation of how much that floor surface has changed over time. Cash allowance is appropriate because you only have to spend as much as needed. Or more. Because if the concrete wasn't good to start with, then you've got more that you have to expend from your cash allowance to prepare that floor.
But it comes down to this missing trade scope. Yeah. So easy to repair, so easy to address, and we've missed it. And yet there's skilled workers out there that do that for a living all the time.
Seth: Yeah, there's actually, and I'm sure some people are listening to this and they're like, there's no way there's people out there that are putting aside an allowance to fix floor flatness.
But there is a large retailer, I don't wanna say their name, but large retailer out there that build, builds big warehouses and they actually do that. And that was my first time that I was on a project that had that allowance and they had that trade, that middle ground they had them planned in the in the schedule.
Which I personally thought was shocking. I was like, oh, you're planning on us not providing what you need. But the, yeah, the floor flatness they do have an allowance, but they still. They still expect a high initial, high quality finish.
So they have an allowance. And then, our client they were sharing with us that they were one of the GCs that used the allowance the least across the country. So they wanted to make sure we delivered a high-quality product, even though they did have this allowance to do the grinding of the floor they wanted to make sure we'd still delivered a high-quality product so they wouldn't have to use that allowance as much.
Keith: Yeah, and I've written conditions that's talked to that as well. It basically says, this is not meant to repair work. This is not to say that, oh yeah. We're gonna be, we're gonna be fixing up the floor after the fact anyway, so we'll just slot the concrete down and do what we can do.
We don't have to spend the time. No, you need a good-quality floor to start with. I'll say minimum FF 25 better yet, FF 30. So, we're still pushing that, what's reasonably expected from using standard tools and materials. I should also say American Society of Concrete Contractors also had a position paper.
Seth: Yeah. Yeah. That's says we got, they, we have all kinds of positioned papers. I think there's one, three. Oh, I know. There's 36 of 'em. I like them.
Keith: I like them too. They're great. It's every time I have a problem with concrete, it's let's see what ASCC says. They're paper number six. So, it was an early one says, Hey, you should be doing something about this and coordinating between Division 3 and Division 9.
And oh, by the way, you, me, the way you guys measure things in Division 9 is different than when the way we measure in Division 3. So, you need to, basically the position paper said flooring installers need to be recognized for their tolerances. They're different, they're a lot tighter. They are equivalent to FF 50 to FF 100 many times.
And again, that goes back to this new position paper, best practice for straight edge measurement. It sets up the responsibility to the general contractor to turn over an appropriate floor for the floor covering installers. It recognizes the good work that the concrete finishers did, it brings in and otherwise, unrecognized portion of the construction finishing trade that is always brought into to repair floors at huge expense cuz it's usually an extra to the project that the owner doesn't want to pay for because they expect that perfection, that level of, FF50, or FF 35.
That they're not getting and they're pointing fingers. Everybody's pointing fingers at everybody else. The concrete finisher, I did my job, the floor covering guy saying, it's not my responsibility. GC going, I don't know what happened here cuz you didn't control the conditions.
And everybody not really understanding what, that concrete is. It's a beast, it has a mind of its own and it will do what it will do. You can place concrete one day it'll behave perfectly. The next day. It's a wet, cloudy, overcast day. The guy on the end of the mix truck, he forgets, oh yeah, we, yesterday we added in a lot of water because we had a lot of evaporation.
Today he forgets not to put in so much water, cuz he did the same things he did yesterday. Now we have a permanently wet slab. There are issues all over the place. The trades, they. They're unaware, I'll say, of all of the physics that goes into making concrete, and there's no expectation that they should understand the physics, but we can certainly address those outcomes within the project documents and make sure that the owner, pays a fair price for the work.
We have to get the owners to agree to, of course, the cash allowance in the first place. Large clients. Yeah. Like your warehouse example, without saying a name, we do a lot of warehouse work for a particularly large retail outlet that pretty much dominates everywhere in the world. And yeah they recognize that need for service correction.
They also recognize the need for good work at the outset, that it's, it works well when you have communication between all the trades. Yeah. Yeah. Said that's the thing too. Have Division 3 talk to Division 9. Division 9 says this is what we need. And Division 3 says we'll say, oh if that's what you need, here's what we can do for you.
Rather than, don't blame me, man. I was good on my day,
Seth: Yeah, no it definitely starts at, starts with the owner. And then it, it has to trickle down all the way down. Owner's reps and design team, everybody's gotta be on the same page. That one project I was talking about. That was probably the best pre-pour meeting I've ever attended.
After being in the industry, two decades plus that was the one I actually felt was worth my time.
Keith: For everybody. The fact that you even had a pre-pour meeting, right?
Seth: Yeah. But I felt everybody was engaged. And it started with the owner's rep.
He drove that meeting versus typically we as a concrete contractor we're the one that initiates the meeting. We're the ones that drives the meeting. We're the ones that provides meeting minutes, the agenda, everything. And everyone's just falls along and we're, I don't feel like everyone's engaged, but when it came from the owner's rep, everybody was paying attention.
It was like, this is what I expect, this is what y'all are gonna do. This is how it's all gonna happen. And so everyone knew that, that participated in that meeting knew what to what we all had to deliver. Yeah, so that. I'm sorry, go ahead and then we'll jump to the straight edge thing cuz you said you were getting some pushback on that.
Keith: Yeah. And I was just saying that's one thing the National Floor Covering Association recognized when we were working on harmonizing how self-levelers were installed, where they came in, and who was responsible. The big realization was the coordination wasn't happening, so they actually wrote for specifications.
A coordination section that actually does exactly what you just described, brings the concrete people, all of the people, the formwork people, the mix the concrete mix company the reinforcing steel guys, the finishers anybody that has to put conduit or anything else on the floor piping.
Brings them all together for that first meeting and gets everybody to agree and talk about what they're gonna do in the future. But yeah, that's and if any of the listeners want to see that document we I'll send you a link. It's a really good document and it solves a lot of those coordination issues.
Seth: Yeah, no, that'd be good.
The so the straight edge let's, couple things. Let's talk about when you're specifying for a job that would require this coordination between the flooring and the concrete contractor. What is your, what's your curing expectation? What do you specify in there?
What's best practice?
Keith: Yeah. I have a really, large curing specification to start with. It's eight or nine pages long.
Seth: It sounds like it's not just spray chemical cure on it.
Keith: It's not just spray chemical cure on it. No, that's the last thing. Although if it's a part of a plan, we'll look at it, but, you can't beat wet curing. That's face it. You can't beat temperature control of that slab. If you allow that slab to cool off to below freezing, even though it's attained its strength, you still have a lot of free water within the slab and it tends to expand as it goes below freezing point.
And by the time you reach, zero degrees Fahrenheit, minus 18 in my world. Ice starts to expand. It, it does very bad things to concrete which just upsets everything. So yeah, the curing plan has to be detailed. Most consultants, most engineers don't really understand the curing aspect.
Once they have strength, that's good. And structurally that's fine. It, but it doesn't recognize any of the work that has to be done later for finishing.
Seth: So is it wet cure seven? So I've seen seven days. 14 days. Seven days.
Keith: Seven days. Yeah. So wet cure, seven days instead of three. Check, and check moisture emissions from the concrete.
There's standards for that. They're oftentimes used for flooring. It's a whole different topic. It's about, yeah. Of floors and everything else, and appropriate measurements. There are a lot of really good standards for checking that how the concrete is actually releasing all of that mixed water.
During progress of the cure period, which can be three to four months it's more than the 28-day strength gain that, that most of us are dealing with. When it gets cold say at freezing point just above freezing point, say, 40 degrees Fahrenheit, five degrees-ish Celsius concrete just stops doing what it does naturally.
It, any strength gain, residual strength gain ends until it warms up again. So there's a lot of things. So keeping the, keeping covers on concrete, getting as much temporary heat as possible. Ways to retain heat on the concrete, keeping the, keeping weather up the concrete, keep the snow and the ice and the rain off your concrete because that delays all of these things.
There's so many things that affect concrete and having a good concrete cure plan, I'm not expecting the concrete to be protected, from day one till the very end. But if we could at least extend that protection after the seven day we cure to 14 days, maybe 21 days of protection concrete has had achance to actually mature.
And as it matures, there's less risk of all these other downstream effects on the concrete slab. Yeah. So I would say most engineers, architects, they'll just refer to some concrete standard cure accordance with blah, blah, blah. Contractor says I've got a top-out party I want to get to, three-day floors, lab, pour, get on with it, finish fast and fast.
Is the course the biggest thing that destroys concrete quality.
Seth: Yeah. Usually, it's pushed by the client's schedule too. So trying to meet that or exceed that. And then when do you do measurement? Floor measurement?
Keith: We start measurements, and I, the GC should be measuring the progress of of how the floor is changing once, once they have access to the floor.
So you have that initial three-day measurement from the concrete trade. Maybe they measure the floor, two months, or three months after. See if how much it is changing. The rate of change can dictate, whether we got a problem or we don't got a problem. And of course, the next point of check would be, at least a month before you're expecting your concrete installer to go on site or your floor covering installer to go on-site because if there are any preparation methods required to correct that slab to a condition that the floor installer will accept, it's gotta be done.
And all the curing, all those materials that you apply to that slab have to be cured as well before the flooring material goes on. So a month before, two months before, we're either good to go a-ok or oh heck, I guess we're gonna have to dip into that cash allowance to make things happen.
Seth: Have you seen any of the internal curing products out there has that succeeded in lieu of the wet curing?
Keith: I've had one project where we used an internal cure, concrete mix design. It was for a large industrial slab in a manufacturing facility. It was amazing. Oh my God. Yeah.
Yeah. It was like, it was the Magic cure. Yeah. So internal concrete cure, it, it addresses a lot of those issues. And again, if you have issues with not maintaining temperature and protection after the fact, internal curing can have just as many problems. That's what I was gonna more money for, but the fact that, the internal curing has its own moisture source.
Seth: I gotcha. Yeah. So it. Yeah. So it can take the place of wet cure, but we still need to take care of the ambient air around the concrete is what you're saying.
Keith: Correct.
Seth: Yeah. I gotcha. Huh. And then you're measuring the measurement.
You, I know the white paper that you sent me, you said people weren't excited about it cuz you were talking about the straight edge and everything. But you mentioned too, you were okay with 3D, that 3D scanning which we've, we do we utilize and we actually that project I was talking about before was the first time you used it and it shows everything.
You gotta prepare to see everything.
Keith: Yes.
Seth: Yeah. Sometimes it's overwhelming for clients to see, everything. They don't know what to do with it. But the, like you're saying, the remediation guys that come in before the flooring guy or whatever is being done after, afterwards.
They, at least in, in my experience, they utilize that data. They knew where the high spots, low spots were, and everything like that.
Keith: Yeah. It's kinda like a cut-and-fill exercise at that point. Yeah. And again if the concrete is being put down, with as carried attention, we're usually talking, a couple of millimeters of correction.
It's not a big deal. Yeah. And it's not pointing fingers at anybody. It's just work that's necessarily is it's necessary to be done. Always has been. We've just missed it, which is why people get upset. And that goes back to the straight edge because a lot of concrete finishers, they fought long and hard to get recognition of this new, the new now, which is now 25, 30 years old, ASTM E1155 or the other one for the Surface Waviness index, FFL and surface Waviness same machine, same little both measures, both.
And of course, they're, they don't wanna go back to a straight edge measurement. Of course, everybody thinks is that old-fashioned straight-edge measurement, which really was designed to show the floor to his best advantage. It really was the pigs here. So, purse kind of comparison.
You take the measurement in one place, in this one place, and it looks beautiful everywhere else. It can look like the Sahara Desert full of sand dunes. Doesn't matter as long as it's perfect in that one location that you place the measurement stick. That's not what we're advocating here. And I and so one of the things I'm trying to encourage concrete finishers to do before they say we don't want no straight edge, and that's the words we hear isread the new procedure. It's best practice. It really does mimic exactly what the 3D laser scanner provides. It just does it with really basic tools, so you can do it, you don't wanna be on your hands and knees with a 10-foot straight edge in front of you, covering, yeah.
The hundred thousand square foot warehouse. Lasers are really good for that. You have a smaller area, a couple thousand square feet. The straight edge is really practical, really easy to use. Find all the same dips and hills. But take a piece of chalk.
You can just draw where those high points are. And then the dry finisher, if you, that's what I've been calling the concrete dry finisher goes in with their, the granny machines. Skip, skip bumps everything off, planes the surface, whatever term you want to use. And it's very easy to convert a not bad floor into a almost perfect floor that's ideal for the floor covering people.
They apply their own skim coats and things like that to do what they need to do to enhance their surface bond, and everybody goes home happy. Yeah, that's the thing about it is once you recognize the missing component of work, it's slap yourself on the forehead. I'm getting a very flat forehead these days, by the way, all the time.
Hit myself on the forehead. It's crazy. It just made it so obvious what needed to be done. And it's one of those things where cooperation between Division 3, Division 9 has come up with a solution that addresses all of the problems. We'll find some new problems, no doubt, but it addresses the common problems that we're currently encountering and stops making people scapegoats for the quality that everybody expects.
Seth: I think that's a good summary of what we're talking about today. So, I think it's a good spot for us to end today. Keith if folks wanna reach out to you, what's the best way?
Keith: Best way is the company I work for is Dialogue. It's an architectural engineering urban planning company in Canada.
My email address is KRobinson@Dialoguedesign.ca and I'll send you that link so you can include that on the bio Yeah. On your website. And I'll also send you along a couple of links to the National Floor Covering Association where the white paper is stored. It's free to download. It's one of the documents that don't have on a paywall because it's kinda like Volvo's seatbelt.
Why patent something that's gonna save everybody's lives? Yeah, and I'll also send you a link to the other coordination documents. So, there's a couple of really good documents there that'll help everybody out.
Seth: I appreciate that. Yeah, we'll share that with everybody and then on our newsletter as well, so that hopefully we can get this be proactive again, seems to be a common theme on this podcast being proactive.
Keith: I love it when everybody works together.
Seth: Yeah. All right, Keith. Thank you. I appreciate it. Thanks, sir.
Keith Robinson, recently retired from DIALOG, is a respected leader in the specifications field with a career spanning almost four decades. He has worked on projects globally, including in Canada, Cuba, Egypt, Japan, and Costa Rica, and has been instrumental in setting high standards of specifications excellence. Keith is known for his innovative research and development of unique documentation for the construction industry, and his commitment to educating the next generation of specifiers. A strong advocate for sustainable construction, he has contributed to numerous LEED®-certified projects and believes in the power of informed engagement and shared decision-making in achieving project success.