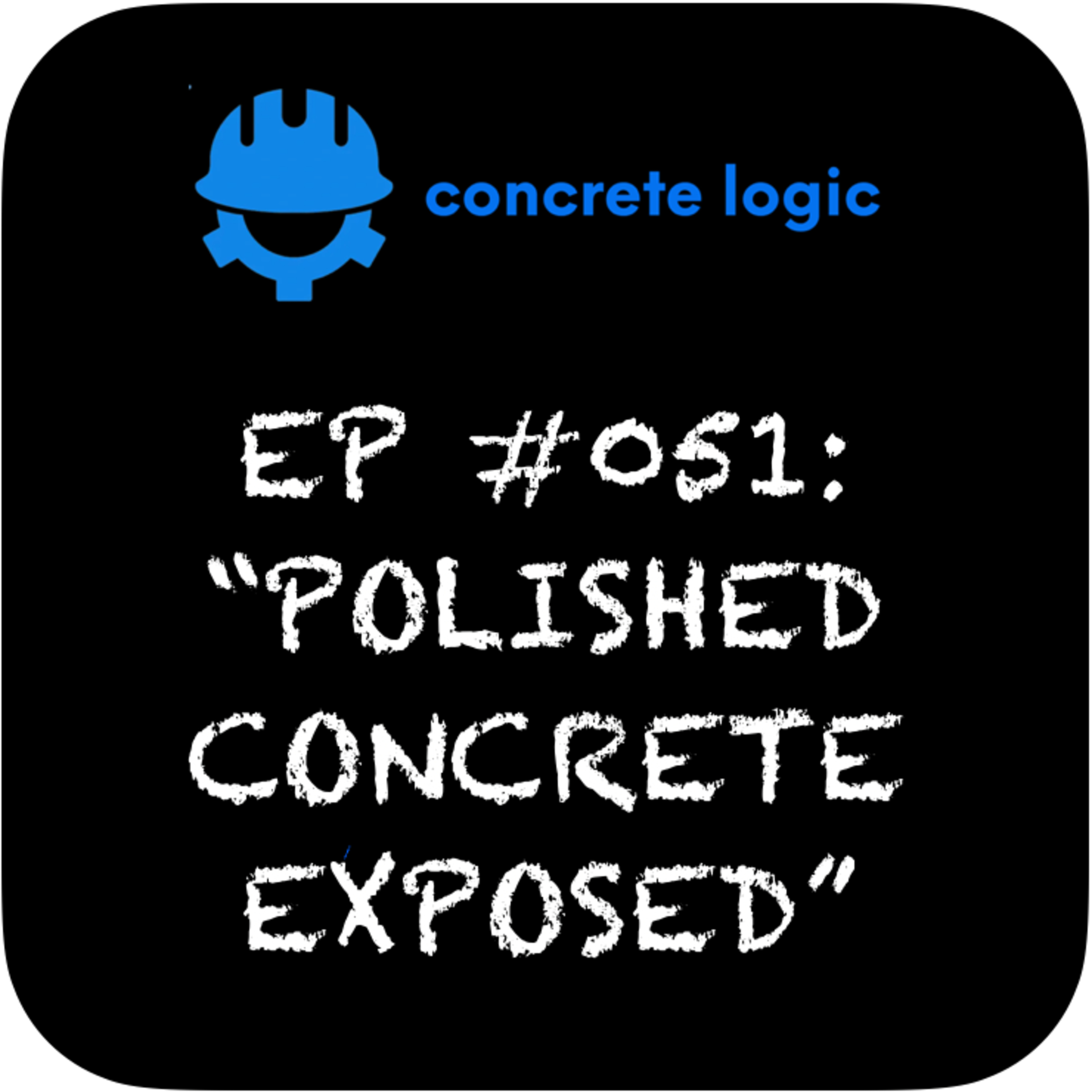
Are you curious about the untold truths and challenges of polished concrete in construction projects?
In this episode of the Concrete Logic Podcast, host Seth brings back guests Keith Robinson and Chris Bennett to dive deep into the world of polished concrete. Architects, engineers, and specification writers will be captivated as Keith, a specification writer from Edmonton, Alberta, and Chris, the CEO of Bennett Build in Portland, Oregon, unravel the misconceptions surrounding polished concrete versus resinous coatings and shed light on the crucial aspects often overlooked in the decision-making process. Get ready to gain valuable insights and expand your knowledge in sustainable construction projects with this must-listen episode. Episode References Guest: Keith Robinson | DIALOG | krobinson@dialogdesign.ca Guest Website: https://dialogdesign.ca/
Guest: Chris Bennett | Bennett Build | chris@bennettbuild.us
Guest Website: https://bennettbuild.us/
Producer: Jodi Tandett Become a Producer: https://concretelogicpodcast.com/show-support
Music: Mike Dunton | https://www.mikeduntonmusic.com | mikeduntonmusic@gmail.com | Instagram @Mike_Dunton
Host: Seth Tandett, seth@concretelogicpodcast.com
Host Website: concretelogicpodcast.com
Seth (00:00.814)
And welcome to another episode of the concrete logic podcast. And today I got two returning guests. I got Keith Robinson and Chris. I'm going to butcher name Bennett. Uh, and, uh, guys, if you could, uh, we'll start with Keith. If you guys could remind our listeners who you are, what you do and all that good stuff, maybe where you're from too. Cause we, you guys are, uh, from different parts of the country or the continent, I should say.
Keith Robinson (00:27.515)
Yeah, Keith Robinson, I work for Dialogue. We're a company of architects and engineers. We design everything from commercial institutional buildings to bridges and other infrastructure. I have a great deal of experience with concrete. My wife always tells me, don't get them started. And here you are, you're getting me started. And it's probably good for a broadcast called Concrete Logic.
Keith Robinson (00:56.04)
I am from Edmonton, Alberta, but we have offices all across Canada and in the United States. So I speak from both sides of the border.
Seth (01:04.703)
Cool. Chris?
Chris Bennett (01:08.148)
Yeah, my name is Chris Bennett. I'm the CEO. Yeah, can you hear me?
Seth (01:09.81)
You there, Chris?
Chris Bennett (01:16.04)
Can you hear me?
Seth (01:17.022)
Yeah, go ahead.
Chris Bennett (01:20.508)
Chris Bennett (01:46.552)
specialized owner representative to make sure that they're getting what they pay for the first time around, right? So that the rendering looks an awful lot like the final outcome and vice versa. We work all over North America. We don't have as many offices as Dialogue, but we are working on both coasts and up in Canada. And I am headquartered here in Portland, Oregon.
Seth (02:17.15)
All right. And we won't hold that against you, Chris. Uh, so, uh, fellas, you guys, um, come or coming on today and, uh, I was sharing with you, we just recorded a podcast, uh, recently, uh, with a Polish car, uh, contractor, Polish concrete contractor, and you guys kind of come at a different angle as far as Polish concrete, your consultants. Um, you guys kind of see, uh,
Seth (02:44.746)
you know, from the beginning to the end, as far as polished concrete goes, specifying, put in the drawings, design, all that good stuff. And then you get to see the end where before we hit record, Chris was sharing a story and you can continue that story about it getting ruined or as as folks are moving in. So if you guys want to get a start, Keith, do you want to start us off or Chris? What what you guys
Seth (03:15.178)
want to tackle today as far as polished concrete.
Keith Robinson (03:22.011)
For me, as a specifier, I deal with the designers, interior designers and architects that have design vision. We discuss finishes well in advance of projects actually going out for bid and construction, go through the entire process of material selection with our client, the owner of the building's interests in mind. We tell them what the performance attributes are, life cycle costs.
Keith Robinson (03:50.783)
all the things that go into making wise decisions when you're spending somebody else's money. And oftentimes we'll arrive at, for an appropriate finish on concrete, sustainable, environmentally friendly, durable, resilient, and we, as a design aesthetic, polished concrete is one of those desirable finishes in the sustainable building.
Keith Robinson (04:16.343)
frequently those decisions are overturned at some point during the construction process either because the bidder, the successful contractor, didn't award to a concrete polishing outfit. That is concrete polishing being grinding and treating the surface to bring it up to a high luster with a very fine slip resistant finish. It's environmentally sustainable. We don't put a
Keith Robinson (04:45.959)
And then we get a substitution request. Can we use a resinous coating? Epoxy, polyurethane, polyuria, something which is other than polished concrete, still provides a nice shiny finish, still provides a look that the architect or the interior designer is looking for, who may not understand what they're actually selecting when those materials are offered. And not to take away from resinous coatings, there's a place for those.
Keith Robinson (05:16.007)
and there's a place for polished concrete. So it's not, you know, something is better than the other, there's just more appropriate locations for both finishes.
Seth (05:27.225)
So when folks ask for polished concrete in your experience, do they understand what they're asking for and why are they asking for, I guess, would be a good place to start.
Keith Robinson (05:39.011)
Yeah, I think my sense is they're looking at the end result, which is a nice shiny finish, which is reflective and highlights the ground finish of the concrete, where you can see aggregate and color pops kind of like a rustic terrazzo.
Keith Robinson (05:59.487)
Coatings can provide that same appearance. So when an architect or an engineer or an interior designer sees that, they think they're getting the same thing. They don't understand the technical attributes. For myself as a technical person, a material specialist, I would tend to say, well, the resinous coatings would be more suitable in a location where hygiene and cleanliness and the ability to completely seal the floor is a good idea.
Keith Robinson (06:30.027)
say like in a laboratory situation. Polyurea works extremely well in those locations. High traffic areas, not so much because you got a lot of footfalls. It tends to wear out the finish. It requires maintenance down the road where polished concrete retains its appearance for far longer and is far less energy and material is intensive to rebuild that finish when it does start to show its age. So...
Keith Robinson (06:58.587)
Apples and oranges, you've got to consider the long-term performance of these things and the actual environments that are being installed.
Seth (07:06.902)
Yeah. And Chris, do you agree with what Keith's saying? Is that what you see in your projects? Do folks understand what they're asking for?
Chris Bennett (07:17.404)
Um, yeah, I would agree with that very much. So I think the aesthetic, um, ultimately, uh, and it's not intentional, but kind of gets in the way of what the owner is. Usually asking for, um, a warehouse logistics, uh, company isn't saying, gosh, you know, what really is on my mind today are our floors shiny enough.
Chris Bennett (07:45.736)
that's really been keeping me up at night. They wanna know that the rolling loads can, you know, power through that in the abrasive manner, you know, and beat those floors up and that floor is gonna continue to tick. So those floors need to be fully refined. Your retailers have concerns about high traction coefficient of friction. Far in a way more important to them
Chris Bennett (08:14.352)
is, you know, our slip and fall case studies providing safe walkway surfaces, then, uh, how shiny something, something is or isn't. And unfortunately with a lot of the, uh, particularly with what I see down here, uh, in the States is you have a lot of language, um, benchmark language that's primarily the, you know, the originated from, uh,
Chris Bennett (08:43.4)
suppliers, where as long as you're reaching that aesthetic, then it gets defined as polished concrete, whether it actually is or it isn't. And Keith, now this is starting to change. There was kind of a big swing where I would say, most of your major firms unknowingly were specifying substitutions and then defending them with their own documents.
Chris Bennett (09:10.512)
Um, particularly if they were only focused on distinctness of image or gloss, sort of these visual sort of, uh, benchmarks, uh, but you're starting to see a swing back. Um, sustainability is a big reason. And Keith mentioned this, you know, with a polished concrete floor, um, and Tim Blankenship, your guest yesterday. And I had talked about this that, you know, um, in, in my opinion, and I think a lot of others, if you're.
Chris Bennett (09:39.7)
polishing the physical concrete itself. That's, it's like a degree of refinement. And so the concrete's in a plastic state. And therefore you're using the materials, the slab itself to produce that floor. Whether it's an existing slab, certainly if it's brand new, and that the carbon footprint, the energy, the material, the economic cost would be using what's already there versus, you know,
Chris Bennett (10:07.92)
What's your term, Keith? Doping the floor. I've always liked that one. Doping the floor with other things just because they've got a shiny aesthetic provides a lot of benefit, whether you're counting carbon calories or your checkbook at the end of the month.
Keith Robinson (10:26.791)
Yeah, I think the informal term is schmoo. Put the schmoo on the floor, you know?
Chris Bennett (10:32.532)
The magic shmoo 5000. Yeah. And it's, it's a big problem too. Because with these wider, very, very broad, forgiving definitions, um, you've got a lot of suppliers that are, do not have polished concrete systems and on their box, on their buckets of shmoo, it'll say polished concrete. And so it's kind of like, well, give me a break. How is an interior designer?
Seth (10:33.807)
Yeah.
Keith Robinson (10:37.715)
Yeah.
Chris Bennett (11:01.144)
on top of maybe not necessarily becoming a material scientist. They've got to be aware that even some of the information they're getting, whether it's malicious or just convenient for marketing, isn't always exactly what they think it is. So it can be a conundrum.
Keith Robinson (11:22.855)
Yeah, yeah. And I think that's, you've hit the point there, Chris. And we see this in all materials. And the concrete industry, as we've discussed in the past, Seth, is kind of replete in naming things because of familiarity, then, by the functions that they actually do. We have a whole suite of products for sealers. They call them sealers.
Keith Robinson (11:47.931)
surface sealers, we've got cure seals, we've got cure hardeners, we've got densifiers, we've got hardeners, we've got a whole suite of liquid applied products that to a person who isn't involved in the concrete industry can all appear to have very similar outcomes and nobody really understands what they're used for unless you educate yourself and become more specialized in that knowledge.
Keith Robinson (12:14.151)
you know, fortunately, most of those things are all covered by different ASTM designations, which says a sealer does this, this, and this, which is very different than a cure seal that does this, that, and the other. You know, so you can derive direction through the performance standards associated with the product, but that same performance attribute or performance criteria is not described in a standalone standard for polished concrete, which is why we end up with this.
Keith Robinson (12:41.895)
Well, if it's shiny and it looks good and has high reflectance and mirrors the ceiling, then that's the look I'm looking for. Therefore, it is OK. That's what I'm looking for. Not realizing that perhaps you've just added 10 years from now a maintenance cost to the owner, which is three or four times higher than the initial installation cost. Not to mention.
Keith Robinson (13:09.823)
probably six to eight times higher than if they had just gone with the finish that had been intended for that area, which is a part of that manipulative misinformation campaign that Chris was alluding to. Nobody talks about future maintenance. Architecture suffers from a lot of ugly out scenarios in all finishes. Oftentimes we're...
Keith Robinson (13:37.787)
Materials are still serviceable. They're replaced just because they've been trafficked and They just don't look as nice as the day they were installed So something which has a 20 to 25 year lifespan will oftentimes be replaced or overlaying with something else Losing if you like that carbon contribution of the original finish that was in place just because it doesn't look good It wasn't maintained properly or perhaps it was
Keith Robinson (14:05.819)
not appropriate for the location where it was installed.
Seth (14:10.194)
Yeah. So how do you guys fix that problem as far as the, or try to, at least as far as making them aware of, of the maintenance of, um, polished concrete or any other product? Do you, do you guys, you guys are, you guys are specification gurus. Do you add anything to what you traditionally see in a specification as far as a maintenance program or anything? I know like.
Seth (14:40.038)
In its traditional spec, there might be some language in there, but usually at the end of a job, a general contractor or construction manager turns over this big old manual and it's got the maintenance program and the owner's owner's manual and all that stuff in there. And they hand it over so they can get the retainage and, uh, probably I would say nine out of 10 times. Those books don't get cracked open until.
Seth (15:08.494)
there's some kind of emergency or something. But there's definitely no maintenance program built on an owner's manual that's turned over after a building's complete. Have you guys had success in the past of getting that in front of the owner and kind of opening their eyes to the real cost of some of these things they're asking for?
Keith Robinson (15:23.347)
Yeah.
Keith Robinson (15:31.931)
Yeah, there's an aspect of specifications writing which is maybe not as common. Most specifications are focused only on the procurement and describing the quality of material quality of the execution. I, and Chris, we take a slightly different approach. We really get involved in the administrative requirements, spell out what meetings have to happen, between who so you can coordinate different parts of the work more effectively. It's
Keith Robinson (16:00.311)
almost stepping on the toes of the general contractor who is in control of the work, but in fact to maintain the quality of materials, quality of workmanship aspect, and the end result that we promised to the owner, the architect really needs to step in and say, we need to have these meetings to make sure that we're actually getting what we've designed. So administrative requirements, which is a part one requirement for specifications, specifications are divided into three parts, general kind of administrative stuff, product
Keith Robinson (16:30.555)
and the execution related stuff. And exactly as you said, Seth, execution can fail entirely the day after the contract is turned over to the owner, if there's insufficient training or insufficient transfer of knowledge. So one of the aspects of part one is saying, we need this information. We need these spare materials, we need these spare tools. We go about creating a maintenance program for the owner with those submittals.
Keith Robinson (17:00.191)
Part three on execution, something called closeout procedures. We will actually ask the people that installed to run an education session for the owner so that they know how, they have hands-on experience on how to maintain those materials. So yes, specification can help, it can educate as well as define what the performance is. So, yes, specification can help, it can educate as well as define what the performance is. So, yes, specification can help, it can educate as well as define what the performance is. So, yes, specification can help, it can educate as well as define what the performance is. So, yes, specification can help, it can educate
Seth (17:24.914)
Yeah. And I've seen, I've seen people in the past, uh, do, uh, video recordings of those trainings so they can go back and reference them back. Maybe they put them on YouTube now. I don't know. It's been a while since I've been a part of that, but, uh, yeah, that, that, that's, um, that, uh, focus on maintenance. Um, I think is we don't.
Seth (17:50.002)
It's just like concrete. I mean, we, we, we push, uh, for folks to build with concrete because we believe in the durability of concrete and it lasts for years and years and you want to replace it, but it's just, everyone has such a short term, uh, uh, outlook on things and they don't think, Hey, how much am I going to be spending on this, uh, epoxy floor for the next 10, 15 years versus if I just did a polished concrete floor or something like that, um,
Seth (18:19.33)
I, uh, in the past, I, when I was, uh, I purely built parking garages, used to do a maintenance manual and in the, in the front of the maintenance manual, we used to do like a Gantt chart. And it said, you know, every two years, you need to do this every five years, you need to do this every 10 years, you need to do this and try to put a dollar amount on it so that's in front of them. So they understood what that cost was. Um, something like that. If.
Seth (18:48.638)
I think that's some kind of graphic or something. I think that would help people instead of flipping through, you know, I've seen some of those, uh, manuals that they turn over to the owners after a building's done. I mean, it's six inches thick. They're not going to, they're not going to read through that. Um,
Keith Robinson (19:05.1)
It's like your grade nine health class where they're teaching about human biology, right? They give you the book and they say, go away and read this and then you're expected to go and become a responsible adult.
Seth (19:18.736)
Yeah. The one thing I do want to ask you, we got on a bit of a tangent there on maintenance, but as far as polished concrete, is the hardener application, is that a requirement to do polished concrete? Is that every polished concrete floor, there's some kind of?
Seth (19:36.962)
hardener or whatever material put on first and then, yeah.
Keith Robinson (19:40.199)
Densifier, yeah. Yeah, that's essential. You've got to close off the micropores and surface structure of the concrete. You've got to kind of get it so that you're not absorbing. And there's different materials, different quantities of the actual reactive components within those products that the specifier, the contract administrator, the architect, or the designer needs to be aware of. You want to create the highest percentage of solids.
Keith Robinson (20:09.727)
to consolidate or densify that surface. So again, you can get a less expensive product that might require reapplication after five years because as it's trafficked, you just wear off that very thin layer of reactivity or something which has a deep penetration and you can walk on it for 20, 25 years before you need reapplication.
Chris Bennett (20:34.344)
I've seen there was a project with a well-known brand where it was like 2 and 1 half, 3 million square feet, where they densified, I want to say, a total of four times before substantial completion because of not having the right tools for the toolbox, so to speak.
Chris Bennett (20:59.608)
And so it can be one of those issues certainly for long-term life cycle and maintenance. But I see particularly with a lot of your, you know, and densifiers are all mostly water at the end of the day, but the more mostly water they get, you know, the less effective they are, obviously. I also wanted to add in something
Chris Bennett (21:30.432)
designing in the maintenance and starting at initial installation, if I could just real quick, because they're related. One of the things that we certainly don't exclusively do it. A lot of people use surface microtexture measurements, average roughness, RA. We use that for placement and finishing, for polishing.
Chris Bennett (21:56.088)
not just because it'll give us some sort of quantitative measure of the smoothness, are you actually refining the floor or are you just, you know, coating it with shmoo, but because you can set your coefficient of friction maintenance for that. And rather than kind of have guesswork of like, hmm, are we still at high traction coefficient of friction? I know that if I'm maintaining, you know, like a 30 to 10 micro inches,
Chris Bennett (22:24.992)
that I'm going to be hitting that high traction coefficient of friction. Um, and so I think one of the, I think there'll be two things that fundamentally change polished concrete. One of them is the safety aspect. Um, it's really hard to program different types of coatings, um, and then maintain coefficient of friction with something that's going to be changing in thickness, uh, and texture and things like that.
Chris Bennett (22:52.428)
But if you're physically refining the concrete, it's very, very easy to do. And the other one would be that you're getting a lot more finishers these days as people are figuring out how to do polishing underneath their trowels. You're gonna get a lot of guys that really understand concrete curing and finishing. And again, ultimately that's what polishing is, is a really high level of finishing that understand concrete.
Chris Bennett (23:22.328)
and understand refinement. Most, not most, but a large portion of your concrete polishers out there aren't like Tim Blankenship yesterday, where they came from a placement and finishing in a concrete background. A lot of them are Janssan guys. And so that's why you see a lot of polishing mobilizations kind of at the end of a schedule, because they're installing it, the whole paradigm for them.
Chris Bennett (23:51.872)
and a lot of general contractors is it's a floor coating or covering or something you do to the concrete, not the concrete itself. And again, it goes back to what are you trying to do? And it should be serving the client, making sure they've got that durable floor, making sure it's got high traction, coefficient of friction, making sure
Chris Bennett (24:20.672)
within the aesthetic perimeters that's being met for them. And I have found too with RA, that it really helps with contingency expenditure reducing. That we've had a lot of projects where the owner and the bill AEC teams aren't paying any contingency expenditures because we're able to identify substitutions early or if they sort of happen anyway, the owner
Chris Bennett (24:50.516)
isn't the one on the hook for it. I've never understood that, how the owner cannot be at fault, but ultimately has to pay for things sometimes. It's mind blowing. And so, RA is one of those tools, along with coefficient of friction, that need to be average roughness. It's a measure of the surface microtexture.
Seth (25:09.327)
What's, what's RA?
Chris Bennett (25:18.276)
of glass, of metal, of concrete. A lot of times in the concrete industry, there's a handheld stylus devices. Although I know that there are some automated ones, kind of like Zumba's or Roomba's or whatever those things are called that go around and take little measurements. And one of the things that's nice about that is if
Chris Bennett (25:46.472)
If somebody does have a substitution, if they have sort of coded it, that stylus is still going to give you a quantitative measure of the differences between the peaks and the valleys of the microsurface of the concrete. So if it's been fully refined, it's going to be really, really smooth, really smooth if something has just been sort of, you know, clear coded on top of it. Or if maybe there's been a dye introduced.
Chris Bennett (26:14.616)
to a seal or densifier component to sort of hide those scratches, your naked eye or even a gloss meter, something like that, isn't going to be able to tell you that. So it's a very good quantitative tool to be able for project teams to hold on to contingencies, but also in the longer terms of lifecycle and maintaining that floor, not just for hygiene, but also for safety and coefficient of friction.
Seth (26:43.117)
Gotcha. So that average roughness is specified, and there's a purpose for it depending on what type of project it is. Is that correct?
Keith Robinson (26:54.547)
That's correct. That's what gives you that dynamic coefficient of friction. And it's funny, it's probably one of the key differences between polished concrete and say liquid applied coatings. Very highly reflective concrete is not slippery. It's actually because of the microtexture. It actually has very good slip resistance where coatings tend to become slippery when they are glossy, particularly when water or snow and ice are present.
Keith Robinson (27:25.135)
Um, we actually had a large airport client who had a polished concrete floor, wasn't sure how to clean it. And they're actually using liquid soap, you know, like dishwashing soap to rinse the floor and then they, they wet mop it to clear off the obvious suds. But over time you built up the soapy film, which then took away from that. RA you could see that the RA had changed because the floor was no longer glassy had gotten quite dull.
Keith Robinson (27:53.479)
They were thinking the finish was damaged and but they were also having slip fall problems and injury claims.
Seth (28:03.518)
Yeah. Huh. Yeah. That reminds me of my garage floor. I always yell at my kids if it rains outside and, um, at my garage floor, it might be polished. I'm not sure after talking to you guys, but anyways, it looks polished and, uh, uh, yeah, when they come in and you know, their shoes get wet and then they run into the garage and it's just like an ice skating rink and I was, so I always like guys can't run in the garage. If you're, your shoes are wet.
Seth (28:31.766)
But yeah, never thought of that polished floor. So one of you guys hit on something earlier where you were saying the timing of when you're supposed to do polished concrete. So yeah, I assumed you were supposed to do it at the end after everybody mucks the slab all up after the concrete guy goes. Yeah, yeah.
Chris Bennett (28:38.424)
I'll let you.
Chris Bennett (28:55.64)
after it's damaged and has little holes, yeah. That's the kind to do it.
Seth (28:58.666)
Yeah, so you come in and you place finish the floor and then, and then the, uh, all, you know, the, the electrical trade, the HVAC guy, the, uh, insulation guy, he, he's spraying stuff everywhere and you know, the floor gets all screwed up. And then the Polish guy comes in and he cleans it all up. Isn't that the way you're supposed to do it? That's right.
Chris Bennett (29:20.092)
what he needs in a change order first to clean it and then he installs it.
Keith Robinson (29:20.126)
Yeah, that's how she...
Keith Robinson (29:24.871)
Yeah. Yeah. And it's funny because all of those other processes you just named, you know, are detrimental to most finishes that are applied, right? The mechanical guy, plumbing guy, he's in there, he's got pipe cutting oil and all sorts of stuff spilt all over the floor. Electrical guy, they go around with those big fat permanent quickie markers, right? They're marking up the floor and that just, you can never get rid of that stuff. It just translates its way through whatever finish you put on top of it.
Keith Robinson (29:51.803)
In fact, the best time to do it and the most efficient way, cost effective way is to do all that finishing early in the process before you get a lot of encumbrances on the floor. And polish it and then protect it. There are protective things you can put down on the floor. It could be like an adhesive craft paper product. There's liquid products that you can peel and stick on floors. It's a great surface for the people to walk across, protects it from scratches, protects it from all that oil and scratching and
Chris Bennett (30:21.867)
Yep.
Keith Robinson (30:21.895)
Black folk figures and so it's again it's about the timing.
Seth (30:27.218)
Yeah. So you do it how long after the floor is put down? Is it a couple of weeks? Or is it how does that work?
Keith Robinson (30:37.279)
There's a lot of other kind of, I'll say for me, there's a lot of other criteria that are involved, depending on the actual end use of the floors. We might also require super flat conditions for certain hospitals or laboratories, which require additional work to the surface of the concrete. Best time to do that is actually before the building is enclosed. The building is complete, but not fully enclosed. So you can go in and you can...
Keith Robinson (31:03.651)
stage of materials into the building from the side, rather than carting up through the building after it's enclosed, probably the second best time then to do all this material work would be after the building is enclosed, but before all those interior partitions are in place. The worst possible time is to do it exactly as you say, once all the other trades have gone through and you're starting to clean out, now you've got a lot of hand finishing work around the edges, you can't get the big equipment in.
Keith Robinson (31:34.407)
It's far more laborious, far more time consuming, which of course would then drive up the cost and lower the cost advantage of polishing concrete versus putting down the coating, which is probably why coatings get substituted many times because at that point perhaps they start to become more competitive to each other.
Seth (31:56.094)
Right. Yeah, because the polished concrete guy shows up, and he goes, this is not what we talked about at the beginning of the job when I quoted it. Now I got to work inside these little rooms and polish and clean up all this mess and everything. Do you guys know what the cost difference is between doing it when, I guess, when you're supposed to do it, and you have to put down whatever protective layer over the top of the concrete? Because that, to me, sounds.
Seth (32:25.79)
expensive because you got to put it down and there's a cost for that. Then you got to maintain it throughout the project. And then you got to go chase down the trades that damage that and have them pay for, for, for repairing it.
Keith Robinson (32:38.211)
Yeah, the average cost of an actual, yeah, the average cost of an applied finish is probably somewhere between about five to $10 a square foot. Polishing concrete is depending on how much definition you're looking for, $2 to $3 a square foot, putting down your protective layers are probably a buck or two a square foot. They're not overly expensive. There are products on the marketplace. Do I name a product?
Seth (32:46.082)
Uh-huh.
Seth (32:58.542)
Okay.
Seth (33:08.726)
You can. Yeah. Yeah.
Keith Robinson (33:09.989)
You know, Scudo, you know, which is the first one I came across. Scudo is great. It goes down kind of as this pasty kind of liquid. It dries on the concrete surface. It also helps with curing the concrete because it retains moisture. And it's really hard to tear or pull off the floor because it's fully adhered to the floor. But it's kind of like a post-it note in that way.
Keith Robinson (33:34.427)
It adheres well, but when you must just start to pull it off, it peels off very easily, and it's very easy to dispose of after.
Seth (33:41.974)
Okay. So it's a, like a paper type product that you stick out. Like.
Keith Robinson (33:45.307)
It's kind of like a liquid paper that goes down. They've also got memory materials. There are other products out there as well. I just can't, they're just off the top of my head right now.
Seth (33:55.359)
Right, right. Huh. That's interesting. So that's when, so after the concrete contractor places the floor and then the polish guy comes in and does his thing and then they protect it before everybody else comes in and trounces all over the top of it. So that's to protect it. Cause I was going to ask you guys, we've talked, I think I talked to you guys, I think I talked
Seth (34:23.502)
Keith about it and maybe Chris about the, the, having an allowance, uh, for, uh, a gap in, in, you know, after the concrete guy's done and then, uh, uh, flooring guy comes in nine months after and has to deal with, you know, what the concrete has done as it, yeah, as, as it's cured over time and, and, you know, might have to do skim coats or whatever to put the floor down.
Seth (34:51.222)
Um, that's what I was going to ask you guys next is it, there's, you guys recommend allowance for the owner to carry, um, but it sounds like the owner might not have to, if they do it the right way, is that right?
Keith Robinson (35:05.731)
Largely, yeah, I think the need for allowances of the type that the floor finisher requires are largely reduced. Because when you're grinding the concrete for polishing, a lot of that surface movement, you know, due to shrinkage and warpage has already occurred as well. It's not going to be done two weeks after the concrete is being placed. It's going to be done two to three months, four months after the concrete is being placed. So much of that surface irregularity...
Keith Robinson (35:34.079)
would have to be corrected anyway. At this point though, instead of being an extra to the actual installation, which would then be covered by the cash allowance, depending on how much it went out, you have to do that preparatory work anyway, so it's built into the cost. So rather than being an extra three to $4, after the fact, it's just a part of the finishing and forms a part of that cost.
Seth (35:58.527)
Yeah, Chris, you had something?
Chris Bennett (36:00.073)
Right. Well, when you're polishing, and I know this is going to be controversial maybe to some of the listeners, like, number one, there is no dry polishing. This is my opinion. Again, we don't have a lot of contingency payouts, and so I think clear definitions help. I'm not just sort of tooting my own horn here.
Chris Bennett (36:27.452)
In fact, there's not a lot of different types of polishing. Um, and if you are actually polishing, it's a wet process. You're returning even an existing slab back into a plastic state. So let's say you've got dry shrinkage crack and you've got pop outs and other little, you know, farts and bad things that you don't like aesthetically, right. Or maybe even that might have serviceability issues by folding that concrete.
Chris Bennett (36:56.044)
back into itself, you're a direct, just as part of the polishing process, you're already in most cases, say like eliminating the, you know, 20 to 30 cent a square foot grout coat that's going to match and be more aesthetically pleasing for the owner and the design teams, you know, because the material that you're trying to match those imperfections with is the concrete itself.
Chris Bennett (37:23.776)
but it's also an element of speed. And I think production, particularly with your larger facilities, Seth, you can't just look at a per square foot kind of cost on products and labor. You really need to look at the construction schedule impact. And we were comparing sort of waiting six months, eight months, nine months later to begin that polishing, while the...
Chris Bennett (37:52.972)
Concrete's getting all banged up and people are having scissor lift, jousting with hammers or whatever else that they do, you know, outside of polishing the floor. But if you can get on a slab like that first day or two to begin your polishing, you know, like the truck leaves, best case scenario, you're polishing 12 to 24 hours later, you know, beginning that process. Or maybe you're removing...
Chris Bennett (38:21.776)
cement because of low carbon. And so you need to, you know, wait three or four days, five days, six days, seven days, something like that, depending on how much that you're, you know, taking out. The amount of operational costs from, you know, shedding weeks off of that schedule, you have to start adding up a lot of different figures, maybe construction loans, whatever that percentage is, how much is a week worth to the owner, the developer, to the GEC.
Chris Bennett (38:51.324)
all of these things sort of compound. So to really fully appreciate the cost difference between a lot of these substitutions and real true polishing can be really significant once you start to tally everything up together.
Seth (39:09.187)
Yeah, huh. Yeah, that's definitely a different way to look at it. I'm sure there's some listeners there that have been thinking that you do the polishing at the end. I know I did before I talked to you guys. So it would be interesting to hear from our listeners if they have any experience of doing it the way. I guess you guys consider the right way of doing it. But the...
Seth (39:37.11)
For today, I think that's a good spot to end the conversation. Keith, if folks want to reach out to you, what's the best way?
Keith Robinson (39:45.263)
They can they can reach me through my email at dialog. It's it's krobbinson at dialog design dot ca And I think that will be in the contact information on your web page Yeah questions I we share specs all the time so if people want to share I That the price of admission to share is usually you have to share something back. So
Seth (40:11.378)
Yeah. Yep. And Chris.
Chris Bennett (40:15.972)
Yeah, you can reach me at our website www.benettville.us or my personal email is chris at benettville.us.
Seth (40:28.618)
All right. Sounds good. Yeah. Folks reach out if you want to talk polished concrete with these guys, their specifications or both. Thank you again, you guys, for coming on the show. We'll do it again.
Keith Robinson (40:41.983)
Excellent. Thank you.
Chris Bennett (40:43.192)
Thank you, Seth.
Keith Robinson, recently retired from DIALOG, is a respected leader in the specifications field with a career spanning almost four decades. He has worked on projects globally, including in Canada, Cuba, Egypt, Japan, and Costa Rica, and has been instrumental in setting high standards of specifications excellence. Keith is known for his innovative research and development of unique documentation for the construction industry, and his commitment to educating the next generation of specifiers. A strong advocate for sustainable construction, he has contributed to numerous LEED®-certified projects and believes in the power of informed engagement and shared decision-making in achieving project success.