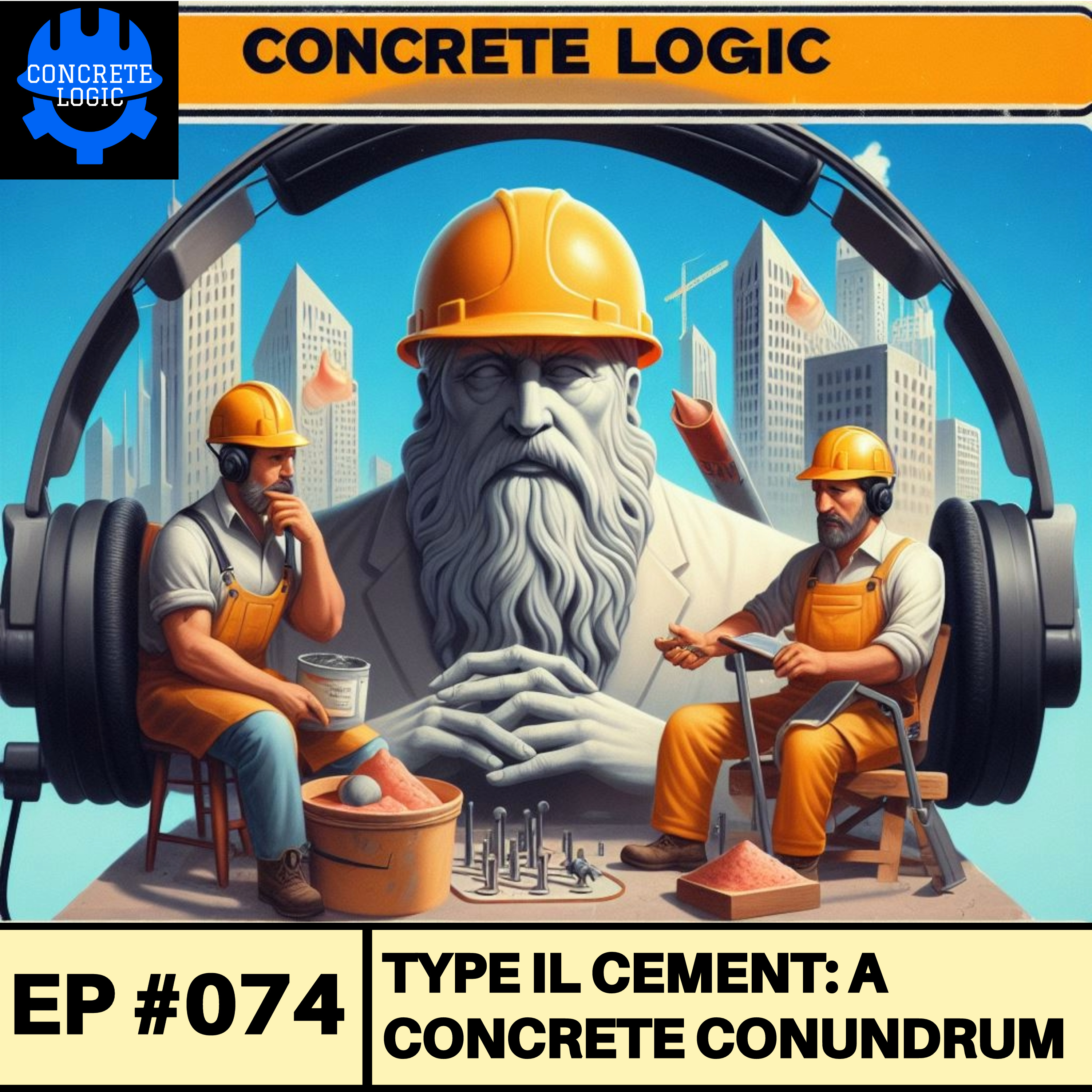
Summary
In this episode of the Concrete Logic Podcast, Kyle Kammer from Concrete Strategies and Seth discuss the challenges and troubleshooting methods related to Type 1L cement. The conversation covers the reasons why Type 1L cement is a popular topic in the concrete industry and the challenges of using it across different locations.
Kyle shares insights into the issues of differential set and cracking, as well as the importance of communication and material variability. The discussion also explores the role of admixtures and the development of new solutions for Type 1L cement. Overall, the episode provides valuable information for contractors and industry professionals dealing with Type 1L cement.
Takeaways
Chapters
***
Did you learn something from this episode? If so, please consider donating to the show to help us continue to provide high-quality content for the concrete industry.
Donate here: https://www.concretelogicpodcast.com/support/
***
Episode References
Guest: Kyle Kammer | Concrete Strategies | kammerk@concretestrategies.com Guest Website: https://concretestrategies.com
Producers: Jodi Tandett, Jace Stocker
Donate & Become a Producer: https://www.concretelogicpodcast.com/support/
Music: Mike Dunton | https://www.mikeduntonmusic.com | mikeduntonmusic@gmail.com | Instagram @Mike_Dunton
Host: Seth Tandett, seth@concretelogicpodcast.com
Host LinkedIn: https://www.linkedin.com/in/seth-tandett/
Website: https://www.concretelogicpodcast.com/
LinkedIn: https://www.linkedin.com/company/concrete-logic-podcast
[00:00:00] Seth: welcome to another episode of the Concrete Logic Podcast. Today I have Kyle Kammer from Concrete Strategies. Kyle is the director of quality. That's it. I'm not going to add any more to it. Kyle. All right. Uh, like I've been sharing with you guys the last, uh, half, you know, handful of episodes, uh, if you would, if you get some value of, uh, Kyle's, uh, episode today, our discussion, and you want to, support the podcast.
I got three ways you can support the podcast. The first way is you can share this episode with a colleague in the concrete industry. the second way is if you go to concretelogicpodcast.com, in the lower right hand corner, there's a little microphone icon there. If you click on that microphone, it allows you to leave me a voicemail and you can give me feedback on the podcast.
If there's a topic or guests that you would like to hear on the podcast, you can also do it that way. You can also just email me at Seth at concrete. logicpodcast.com as well.
The third way is back on that homepage, concrete logic podcast. com and the upper right, right hand corner. There's a donate button. If you get some value out of this podcast or any of the other episodes, you can donate any amount that you feel it's worth. So with that, Kyle, we're going to talk about type 1L cement, a favorite topic of the concrete industry.
Why is that, Kyle? Why do we like to talk about type 1 L cement?
[00:01:33] Kyle Kammer: Well, obviously it's new and exciting. we've had a lot in the industry in general with the change, you know, we're a slow industry, construction in general to accept change. that's a big part of it.
There have been a few pickups along the way as far as material quality and general rollout process that, affected some people more than others. So, obviously that's, been a huge issue over the last couple of years, for much longer than that. certain areas like the Northwest have been using it for, five plus years at this point and they've figured it out. So the rest of us just have to catch up.
[00:02:10] Seth: Yeah. So you were sharing before we hit record that you're, you're seeing well, your job, you're traveling all across the country.
'Cause Concrete Strategies is a national company and uh, you get to see how things are going with the Type one L cement throughout the country, which. We all know, uh, folks that are in the industry that concrete is very localized, uh, product, you know, the, when concrete is, is, uh, produced, it's used with local products in the area and, um, so it's very challenging when we're using a new cement that, the cement folks dropped on us.
So here in the last couple of years, um, to figure things out. Cause you know, one thing, uh, that's going on in, in one part of the country, if you're having issues, not necessarily going to have the same issues somewhere else in the country, right.
[00:03:05] Kyle Kammer: yeah, and honestly, it varies from, area to area, but also, over time, the cement companies are still trying to figure things out.
They had most of them on track. Now, they were also tweaking things on the production end and that obviously trickles down to. The, end user.
[00:03:24] Seth: Yeah. So can you share, you spoke at ACI and you, talked about some of the issues you were seeing and how to troubleshoot those issues.
Can you share some of that? yeah.
[00:03:35] Kyle Kammer: So, we did a mini session that was, myself, Rob Young with Lithko, Ronan Professor from Oregon State, Jason Weiss.
[00:03:41] Seth: he's a, a big name.
[00:03:43] Kyle Kammer: Yeah. That's why there's a weasel and a wise anyway, uh, Ben, Ben works for green umbrella, their chemical company.
So, um, and you know, we kind of tried to tackle some of these issues Obviously, change and issues, people get frustrated and have been a lot of stones thrown for lack of a better term. And, uh, you know, we were really trying to approach it from the contractor's point of view, you know, Rob and I, um,
Present the problems, but also, you know, kind of present, hey, here's kind of the things that we had to do in certain cases, obviously, like you said, it’s gonna be different all around the country. You might have the same problem, but there may be different reasons for the same problem, the things we did to try to overcome those and hopefully head them off next time.
We focused on three main issues, which were cracking, some of the differential settings we've been seeing in, low breaks. low breaks are a big one because That's our method of acceptance, differential set kind of affects our, finishing crews.
And then the cracking piece is, just owners don't like cracks. Everyone wants a crack free floor and, uh, they don't, anytime, you know, most of them see cracks, it seems to, uh, uh, be a pretty big trigger. So. Um, but, yeah, we, we, we gave a few examples of projects around the country, where we're seeing issues and, tried to, look at these things, in your mix design, try some different chemicals, a lot of the admixtures that we have in the industry weren't designed to work with one, too.
It turns out 1L is a different product, so, you were going to have a different reaction compared to what you are used to. And, a lot of those, we ended up having to, go back to concrete before add mixtures and we basically peeled everything out and just put all the water in.
We slowly added things back in to figure things out. the differential set thing was, there's some interesting, reactions with some of the super plasticizers out there. And that one, honestly, it's still kind of a mystery in some areas, but we both, let go in and concrete strategies, both have a few, pretty bad experiences where, we pour this slab, finished it, burned it in.
And then once we rolled the saw cut cart out on there, all of a sudden, the saw cart, breaks through the surface and there's plastic underneath the hard burnt in surface. a lot of that was, trying to remove some of the chemicals and do the things that we needed to do as contractors,
Make sure our subgrade was, okay, it wasn't too cold, it wasn't too hot, and then, you know, low breaks, those are always painful to deal with because, you have to go explain yourself to the owner engineer and you, we got some tolerance.
But at the end of the day, can you accept this even though it's 500 or 1000 psi low it's not a good look for anyone. Um, but we, we had some pretty interesting, uh, projects where we were able to see the, the mix transition from 1 2 to 1 L, in real time, we were seeing decreases in strength, off of mixes that we had been using for years,
Obviously, there's a reason for that when something changes and, you know, all of a sudden have a bunch of issues and it's kind of, kind of easy to pick out that 1 change. It wasn't necessarily just because of the material changing. It was also because we weren't adjusting the way
We're handling it when things change, we change the way we do things as well. And that I don't think was. I don't think we were necessarily ready for in the contractor side of things. Um, but we, you know, again, we're trying to get over this as much as we can, a lot of the big issues there.
we're more communication related. we've had several, suppliers switch their source, but they never communicated that to us. They just, you know, batched it with. They just replaced, you know, hey, we got 560 pounds of this.
We're going to change 560 pounds of that. So it's going to work the same way. Um, well, it doesn't necessarily work like that. Like I said, it's, it's a different material. So, um, we, we gotta be ready to treat things differently. a lot of it, I think goes back to the, the variation and some of the material sources.
Um, and, you know, concrete strategies is a part of Clayco, and Clayco has a very robust, uh, quality control program, uh, system department, and, um, they do a lot of, data tracking with, many of their material sources, specifically concrete, we were able to get into that database and start looking at some of the, Material chemical properties that, um, you know, are listed on the, on the mill certs, but they got a full time data entry guy or 2 that are basically just putting these things in and.
We were able to see some interesting trends and massive variability from source to source, supplier to supplier, but even, month to month with the same supplier, same source. We were seeing, significant jumps in a lot of the material properties.
When you change one thing from month to month, that's, going to affect you on the backend. The blame numbers were a big 1, but we just, 1 l limestone. So a little extra limestone in the cement. We were seeing significant swings in the limestone percentage.
Obviously, the limestone, crushed limestone is going to act differently than clinker will. that was, just trying to diagnose the issues and, head off problems in the future. We definitely learned the value of looking a little closer at our mil certs, trying to get updated mil certs, which, we always probably had done, but maybe didn't focus on it as much as we should have.
[00:09:02] Seth: Were you seeing a, when you were looking at those mill certs, on the cement. You mentioned the limestone content, were you seeing a big swing in the percentage of it? Is that what you were saying?
[00:09:16] Kyle Kammer: Yeah, so, we looked and obviously everybody's going to make their product a little bit different.
Like you said, they're dealing with local materials. The limestone they use to make cement in Florida is not going to be the same as in Missouri or Washington or California or Maine, or Canada for that, that matter, uh, let alone some of the, uh, you know, outside sources.
I mean, we got, we have a lot of imported cement in, uh, in the U. S. from, places like Turkey or Vietnam, but yeah, we've seen the entire gamut. We've seen 6 percent limestone content. We've seen 15 percent limestone content everywhere in between.
The ASTM that the 1L falls under allows you to go up to 15%. The old one was 0 to 5. And that's one of the challenges of us, working across the country, it's not like we're dealing with one material source and one concrete supplier all the time we're dealing with new folks that we haven't worked with before.
And so it's kind of hard to tell what to expect when, you know, you're, you're used to seeing an 8 percent limestone content over here, go do a job in Florida and I've got 14. 7, is that going to be different? probably so.
[00:10:24] Seth: I guess when you're working through this and you're troubleshooting this, do you find it, it falls on the ready mix producer or does it go back to the engineer who did the mix design requirements?
[00:10:37] Kyle Kammer: So that's kind of a complicated one. A lot of it has to do with communication. Uh, the one L is, is a different material. it's a change in materials. That being said, our mix design is now changed if you've changed from 1, 2 to 1 now, and that was probably the 1st. The major communication issue that we were seeing was, um.
It was kind of the assumption early on. And it was kind of the selling point. Like this isn't going to be any different, right? We're going to have a one-to-one replacement.
Whatever you have here, it's going to be the same over here. And I think a lot of the ready mix suppliers, maybe the more local guys were. You know, they had to take that at its word because they don't have a big lab with a bunch of QC personnel to do their own testing and trial it.
So, they just did that, and, in several cases, we're not told and all of a sudden, you have a whole. Slab bore that is a different color or doesn't finish correctly or finishes slower, sets slower, sets faster, there's a range of different, issues or changes we were seeing and they're not necessarily issues, but definitely changes.
The first thing, was an issue, but we didn't know what to expect, from the contractor side of things, because, you know, we just, we heard about this, okay, well now. They say it's going to be the same, should be the same, but, when it turned out not to be that, you know, obviously that kind of caused a lot of heartburn.
[00:11:54] Seth: the communication was one way, coming from the cement producers. And going to the ready mix guys, and then we were hearing rumblings from the ready mix guys, the producers saying, Hey, this is going to change, but there was no, like, what, what does that mean?
And like, and like you mentioned that that was the, the PCA, um, I mean, I, we can go back and find communication and documentation of them telling it, it was a one for one replacement and that's what everybody went by.
[00:12:24] Kyle Kammer: I will say, there’s been a lot more movement. I'm not trying to pile onto the PCA.
There's been a lot of really positive movement from them, to try to get back and address the issues of late. And there were some cement suppliers that really did it the right way. I'll kind of throw a wholesome out there as a good example. At least the wholesome mill in our area, they basically sent a notice out to all of their customers.
A couple years ago, we're gonna change from this to this in six months Just a heads up come get samples. we'll help you out with any tweaks You have to make your mix designs And, it went smoothly. knock on wood, we really hadn't had any issues, from the wholesome, group, the wholesome mill that we use for a lot of our material or our, ready mix in this area.
We had one minor issue with it, but, they communicated and were upfront we called a Ready-mix supplier, they got Holcim on the phone, and the next day, both of them were in our office saying, hey, let's try to figure this out, what do we need to do, whereas that didn't happen with a lot of the other suppliers, I don't think Holcim was part of the PCA, but, some of the bigger players within the PCA have been taking that to heart and, CEMEX and some of the other ones that have, reached out or, done their own investigations into some of this stuff and trying to solve issues.
[00:13:41] Seth: So. you can't say it's new anymore. it's been around for a while, and everyone's switched over now. What are you seeing? So, most
[00:13:52] Kyle Kammer: So I know Phoenix has not, that whole area.
Sulfate ASR issues, you know, with the soils down there, I don't think the 1L has gotten certified, or it might have, but it would have been just recently. I know none of our current jobs down there have any 1L, and so the Type 2 5. Sulfate resistance, obviously it's kind of critical down there. there's a couple of other areas of the country where it's similar to that.
Interesting like California, which I would have thought would have been the first ones to jump on the one L train because of the sustainability angle. But I think they were less than 30 percent of the cement in California was one L. I don't know what. The issue is there.
Certain areas of the country are fully adopted 100 percent and then certain areas aren't.
I know some of the northeast, sources are, and then some still import 1 2 from Turkey or other areas, Cement Quebec I think has switched over just recently, it's an interesting barrel we've got, because, like you said, it's not the same everywhere, that adds to the challenge with, you at Baker, and me at Concrete Strategies, Some of the other larger players that do work.
Various areas of the country, you know, you can't make any assumptions about anything acting the same. Yeah.
[00:15:05] Seth: let's talk about troubleshooting, go back to troubleshooting. So you're troubleshooting, let's say low breaks and usually low breaks, the, the solution is, uh, add more cement. So is that what we ended up doing?
We added more type 1L cement?
[00:15:21] Kyle Kammer: some, in a couple of cases, yeah, but even if it's all 1L and you've been on 1L for the entire. Uh, duration there, there, you know, 5 to 15 percent is a pretty big window to hit in the M at ASTM.
We have one case in particular, where we had a very high limestone cement. And, the gradations of the cement are now becoming important, we had a 4, 500 PSI paving mix.
It was in Virginia, down south we were struggling to hit 4, 000 PSI at 28 days. With 840 pounds of cement dishes, 600 some odd pounds of cement and, the rest was fly ash. in the olden days, that's an 8000 7, 8000 PSA PSI mix.
And we're struggling to hit 4, 000. So we started looking into it. We had to add more water. we had 1 iteration where the management on site, did what you just said. Hey, just add a half a sack. That's all we need to do. And, you know, myself and our materials engineer, I've got on staff here.
We kind of took a look at it. We've already got, you're talking about, having almost 900 pounds of cement. That should be double what you need. so we ended up just saying, leave that cement out and add more water, but it turns out added some water, they played around with the super plasticizer a little bit on the mix end. But, yeah, the water. Helped so in some cases where you have sometimes the higher some higher limestone contents, but not always. It's not always a true indicator, but a lot of times when they're doing that, it's being ground a lot finer.
And so, you can look at your planes. Your blame numbers for that kind of indicates the finest to Some degree the finer your particles, the more surface area you're going to have in your mix that your water needs to coat.
In some cases, we were seeing mixes that just didn't have enough water to fully hydrate, we basically just had to not make any assumptions or say, this is how we've done it in the past.
We're trying to evaluate everything on a case by case basis.
[00:17:24] Seth: was it a higher water cement ratio than you traditionally would, see?
[00:17:27] Kyle Kammer: top down, the whole back. We had a latex, modified overlay on a bridge deck Ended up getting, a mixed design that we've used very frequently over the past several years.
Our restoration division, does most of those overlays and they do all their own, batching, portioning, mixing, and they have been successful with this mix for years. And then all of a sudden, 1L change, and now we're struggling to hit our 4,000 PSI mark at 38 days.
Which is what we were required to get, we even wet cured this, and got low breaks. Seven day wet cure, we got low breaks and huge cracks. In the AMA, low water cement ratio. traditionally low water cement ratio, cured there shouldn't be a crack in sight. but we pulled the wet cure membrane off and it's just cracks everywhere.
And then it turns out the breaks were low, and we ended up having to rip a bunch out and that was an unfortunate sequence of events. We definitely learned some hard lessons there.
[00:18:25] Seth: Are you seeing, any. Admixtures that you hadn't used before that is helping type one L I know you stripped everything down and troubleshoot it from there.
Are you guys finding any other like admixtures out there that you're trying out that you're having success to kind of help out this.
[00:18:45] Kyle Kammer: Yeah, so I know grace.
[00:18:47] Seth: well, don't share anything if you're not
[00:18:48] Kyle Kammer: working on something specifically for use with the 1L as far as a plasticizer.
I'm not necessarily up to date there. That was something that has been kind of pointed out over the last. year or two, the admixture industry seems to be kind of holding his breath and waiting, which, isn't necessarily bad, it was kind of perceived that there wasn't a whole lot of movement from them, which there is, there, there is, you know, obviously behind the scenes, it takes a while to develop new chemicals.
Turns out, there's a lot of good movement there. and I think we'll start to see stuff that's gonna, come out that we can put into our concrete that will help address some of these issues. Terry Harris over at GCP is very engaged in a lot of this. He was at my presentation, really valuable insights, in the discussion portion of it.
Knowing that they are working on it, I'm pretty sure master builders and all the other big players have something, cooking in the works and it's just a matter of, getting it to market.
[00:19:44] Seth: Have you heard of nano silica? Yep. You looking at that?
[00:19:49] Kyle Kammer: we've done some testing, in our yard, like test labs where we're trying out different materials.
the silica is like, dense fires, sealers, things like that, as well as we've done a lot of, uh, I guess, stress testing with, shrinkage reducers, shrinkage comp materials, and, uh, just simple things like evaporation target, uh, trying to figure out which one works the best. And, in certain areas, because they're not all going to work the same, in every area.
We've done a lot of, test labs and really tried to, uh. Make sure that we're not just assuming a materials going to work the same way that it did last year.
[00:20:27] Seth: Yeah. you know, when folks, like you were saying the admixture folks, takes a long time for them to break through.
But I think we're hesitant to use anything new. So, like you said, you got to do some test labs, see what it does.
[00:20:42] Kyle Kammer: it takes a special group to Be that forward. Nobody wants to spend money to try something that won't work.
But at the end of the day, I mean, you kind of have to, I'm not, you know, again, that makes very appreciative of my, my management here. Cause they, they'll, they'll get behind that. They're willing to put up a little bit of cash to try things out and make sure we don't have a problem. Six months on the road,
[00:21:05] Seth: so, it's better than testing it on a job, right?
and what I was getting at is those things, you can't rush it, Unless, you know, a way to make 7 days and 28 days happen faster than the actual time because that's what we're measured by. Right? So, all right. I think we'll pause today.
if you liked coming on here, we'll get you back on and We'll talk some more. but, if folks want to reach out to you, Kyle, and learn about what you're up to, what's the best way.
[00:21:38] Kyle Kammer: you can go to our website, concrete strategies. com, or you can just email me directly.
It's a Kammer K. K. A. M. M. E. R. Kammer, not Kramer, but K. M. M. E. R. K. at concrete strategies dot com. rising tide is going to rise, raise all ships. We can help each other out and the better off the industry.
So, if anyone has any questions feel free to email me. I'm more than happy to take a call or answer an email. I'll help out however I
[00:22:06] Seth: Yeah, we all use the same producers. All right, Kyle. Appreciate you coming on the show, folks. That's it for today. Until next time, keep it concrete.
Director of Quality
ACI Member Kyle Kammer, P.E., is the Director of Quality for Concrete Strategies, the nation’s 7th largest concrete contractor. Kyle also heads up Concrete Strategies’ sustainability efforts and works in tandem with the Clayco Enterprise and large clients to deliver the most sustainable projects possible. Kyle is an active member of the American Concrete Institute and is a member of several committees, including ACI 121-Quality Assurance, several ACI 301-Specifications sub-committees, ACI 306-Cold Weather and ACI 308-Curing.