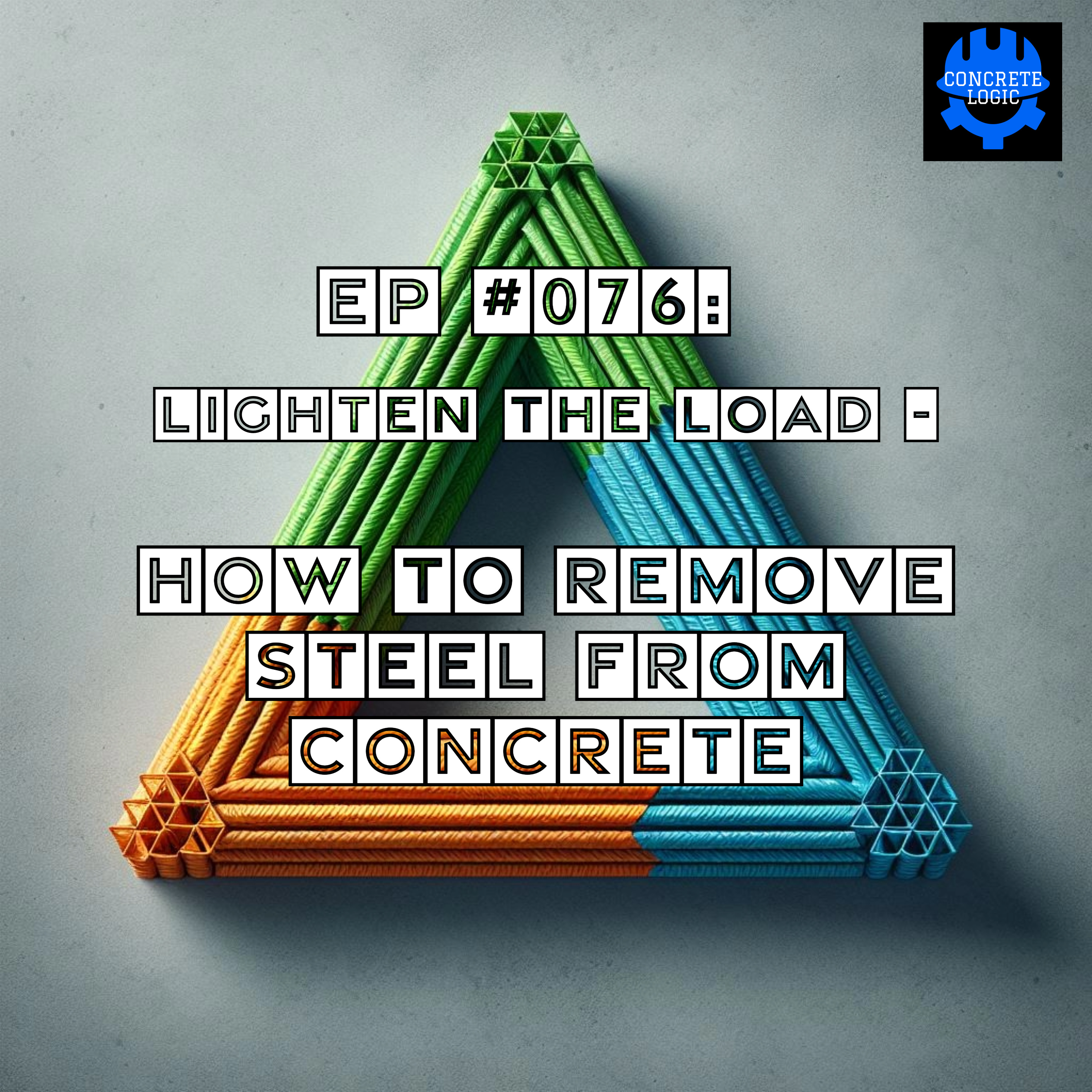
Summary
In this episode of Concrete Logic, Seth interviews Dr. Aaron Fisher to discuss the use of fiberglass rebar (GFRP) as an alternative to steel rebar in concrete construction. He explains the fabrication process and the sizes available for GFRP. The advantages of GFRP over steel rebar include higher tensile strength, lighter weight, corrosion resistance, and sustainability.
However, the adoption of GFRP is still limited due to the need for education and code updates. Dr. Fisher also highlights the limitations of GFRP, such as restrictions in high seismic areas and the need for specialized detailing. Aaron encourages contractors to consider GFRP as a cost-effective and durable solution for concrete reinforcement.
Takeaways
· Fiberglass rebar (GFRP) offers higher tensile strength, lighter weight, corrosion resistance, and sustainability compared to steel rebar.
· The adoption of GFRP is limited due to the need for education and code updates.
· GFRP has limitations in high seismic areas and requires specialized detailing.
· Contractors can save costs by downsizing GFRP bars and taking advantage of their material and labor efficiency.
Chapters
00:00 Introduction and Podcast Support
02:23 Understanding Fiberglass Rebar
05:06 Fabrication and Sizes of Fiberglass Rebar
10:57 Advantages of GFRP over Steel Rebar
19:48 Challenges and Adoption of GFRP
28:21 Limitations and Education on GFRP
36:48 Contact Information and Conclusion
***
Did you learn something from this episode? If so, please consider donating to the show to help us continue to provide high-quality content for the concrete industry.
Donate here: https://www.concretelogicpodcast.com/support/
***
Episode References
Guest: Dr. Aaron Fisher | Ernest Maier| afisher@emcoblock.com
Guest Website: https://www.ernestmaier.com
Producers: Jodi Tandett, Jace Stocker, Mike Hernandez
Donate & Become a Producer: https://www.concretelogicpodcast.com/support/
Music: Mike Dunton | https://www.mikeduntonmusic.com | mikeduntonmusic@gmail.com | Instagram @Mike_Dunton
Host: Seth Tandett, seth@concretelogicpodcast.com
Host LinkedIn: https://www.linkedin.com/in/seth-tandett/
Website: https://www.concretelogicpodcast.com/
LinkedIn: https://www.linkedin.com/company/concrete-logic-podcast
[00:00:00] Seth: Welcome to another episode of the Concrete Logic Podcast. And today I have Dr. Aaron Fisher. He is with Ernest Mayer. He's a vice president of business development, and he's on the show today to help us understand fiber rebar, right? Aaron
[00:00:20] Aaron Fisher: Yeah,
[00:00:21] Seth: fiberglass rebar. See, you already corrected me.
Good job. Fiberglass rebar. Thank you. Before we get started though as I do every episode now is to remind you how this works. So, if you listen to this podcast and you learn something from Aaron today, what I ask you to do it, you can do 1 or 3 three things, or you could do all three things, but the first thing you could do is share the podcast.
So share the podcast episode with a colleague in the industry that would get some value out of this. The second thing you could do is go to concrete logic podcast dot com. And in the bottom right-hand corner, there's a little microphone there icon there, and you just click on that microphone and it's like sending me a voicemail and you can.
Either give me ideas for topics or guests like Aaron here today someone suggested I reach out to him and have him on the podcast so that, that see how that works. And the third thing I almost forgot. The third thing, and the same at the same homepage, ConcreteLogicPodcast.com in the upper right hand corner, there's a donate button.
I click on that donate button and it allows you to donate any dollar amount you want. So if you get some value out of this and you're like, hey, I want to throw some money towards the Concrete Logic Podcast. That's how you can do it. But it doesn't end there. When you donate to the show, the very next podcast episode that is released, you'll be listed as a producer.
And if you want to put that on your LinkedIn profile, on your resume, wherever you want to put it, that is fine. You just put, I was a concrete logic podcast producer. And if someone questions that, you just reach out to me, and I'll back you up. So that's how you can support the show. And with that. Aaron, let's talk about fiberglass rebar.
Not just fiber rebar, fiberglass rebar. So, Aaron, I was hoping you could help us out. Tell us what fiberglass rebar is, where it started, and all that good stuff.
[00:02:23] Aaron Fisher: Okay, so if you're looking at the codes, it's not going to be called fiberglass rebar. The codes call it glass fiber reinforced polymer, GFRP. It has been an academic curiosity for 50 years because of.
We know that glass has high tensile strength. We know that concrete does not have high tensile strength. It has great compressive strength, but low tensile strength. And so that's where we started with steel rebar, steel reinforcing bar, great high tensile strength material. Put the 2 together, you get your nice reinforced concrete.
You get a material that's great under compression and great under tension. But there are some drawbacks to steel as probably most of your audience here knows. Between the weight, the corrosion, those kind of challenges. So, academics and people who are noodling on things said, all right, why don't we see if we can stick glass bars in there?
As you might imagine, glass is a pretty brittle material, so you can't really do just pure glass. Like, you can't have a Pyrex reinforcing bar in there. So, what they did was they actually made a composite material. They took glass fibers and polymer resins. So, the glass fibers provide all the structural strength, the polymer resins hold the glass fibers together, and you move those together, you form them into the shape, and that's actually your reinforcing bar.
It's been a thing for 40, 50 years. The ACI committee that actually looks at this material, which looks at FRPs, has been around since the early 90s, and hopefully nobody corrects me, because I know actually the ACI president, Dr. Nani, that he was one of the guys who founded this committee. And it's progressed along from academic curiosity.
To all right, let's start making some manufacturing. Let's get to the scale. And so now it's a material that's in code. At scale and you can pretty much use it. Anywhere you're using reinforcing bar now the codes aren't fully like, oh, yeah, we can use this every single place that we use steel, but you look globally.
It's gotten a lot of adoption. And so we're starting a lot of see a lot of. International manufacturers come into the US and obviously know that the US concrete market, if you could do it here, the engineers are top rate. And so if the engineers here are willing to use it, that's a pretty good bar for folks around the world.
So that's a little bit about. How long that material has been stewing in the background until it's ready for prime time, which has been a very recent development, actually.
[00:04:46] Seth: I guess just put in layman's terms, the polymer and the fibers and all that's basically a glue that kind of keeps it all together.
The fibers together, and I assume them to make fiber glass rebar, you put in a mold or something, or is extruded. what's that process look like?
[00:05:06] Aaron Fisher: Yep. All right. So I'll get to the 2 questions. So the glass fibers, like the same, so they're like thin glass fibers that you see, same thing that you use in a fiber optic cable, same kind of thing.
You put a bunch of them together and then it becomes like 1. Big mass the you asked, how is it pulled together? So the machine is actually called a pull extrusion machine. So it both extrudes and pulls at the same time. And so as the fibers are held together, and the resin is put there. It cures as it comes out and it comes in a long beam.
So if, like, you wanted a 19 foot run, they just decide, the machine just tells it where to chop. These machines run, like, 24 7. They unspool it, run it through their machine, run it through the pultrusion machine. It comes out and then they cure it and, or they cut it and cure it. I will note, so this is welcome to being a guy who actually has a part of my PhD background is actually in polymer residence.
That's actually what my advisor did. There's 2 basic types of residence. There's your thermo plastics and your thermo sets. Your thermoplastics, that's like your plastic bottle. If you heat it up, it gets soft. Like, it's just a malleable shape. A thermoset is truly a like an epoxy resin. So once it sets into that shape.
Like, you can't heat it up and get it, make it more malleable. Your GFRP bars use thermosets. So, this is one of the biggest things we always hear is like, oh, can I just heat it up and bend it in the field? No, they have to fabricate it to that shape that whatever you want in the factory now being that being said any shape you're coming up with they can do in the factory.
These manufacturers have gotten really gifted at it and it's not some person just standing there being like, I think I got a 90 degree angle. Now, this is all machines that are running 24 7. So they plug it in, they take it out of the CAD. They take off the bar lists and they're just, and then the machines just spit out what it is.
And that's really how this works.
[00:06:56] Seth: Got it. So not too dissimilar to how they fabricate rebar now. Other than it's a different material., I'm talking about the machines and how they fabricate them and the links and everything. That sounds fairly similar to how rebars fabricate. Does it come in the same kind of the sizes like a steel reinforced rebar?
[00:07:18] Aaron Fisher: Yeah, so knowing how to get a product to market is really critical and understanding what the contractor environment and what the engineers are familiar with. They basically copied everything from steel. So, bar sizes, if you want a number 4 bar, that's about a half an inch diameter, they have a half inch diameter.
You want to go up to number 6, that's 6 eighths of an inch roughly, you want They have 1 of those 2 and so exactly how they've done that. And what we've seen with the development actually has been funny enough. We've the manufacturers have followed a very similar art to steel manufacturing, whatever 100 plus years ago when we first really got rebar going the 1st iteration of rebar was just square rods.
And when they started putting that in concrete they realized, like, they got the properties they wanted, but the 2 materials didn't hold together really well. And so the contractors actually had to take the square rods and twist them as they poured the concrete to get more surface area and bond strength until the manufacturers wised up to this and put in integral deformations, which is, you don't even think about it, but every steel rebar is not smooth doweled.
It's Integrally deformed. The GFRP manufacturers had to learn that same lesson over because obviously the first set of bars were just these smooth pieces of polymer resin on the outside. So they were nice. They were dowels. They're great dowels, but they don't have that bond strength you want to concrete.
So a lot of the manufacturers were like, let's rough it up the surface kind of deal. That same idea is like twisting the bar in the concrete. They've thrown sand on the surface. That does roughen the surface up, but what they've learned is that the sand bonds well to the concrete, but then delaminates from the bar itself.
So what a lot of manufacturers are learning very quickly is they need to go to the integral deformation of bars. And so now what is a lot of manufacturers are. I, in my own way, call it a 3rd generation of bars is the integral deformation. So you see, you feel like it's like a rope.
That got hardened, like, it's like a solid rope and so that's a big part of. When we looked at the manufacturers and looked at stuff and looked at the product because we are a distributor. We are not the manufacturer who we were bringing in what we were bringing in. We looked for a bar that had a lot of these material properties that are equal to or better than steel because.
It's really easy to go to a contractor and be like, oh, yeah, I'm used to doing number 4 inch on center. And I go, all right, here's number 4 on center. Like, that does us a disservice. Like, it's a better bar than that. Like, we could probably go to 12 inches on center, or maybe even 16 on center with that same size.
But it's easy to go to a contractor. I'm used to going to eight inches. I was like, fine, just keep doing that. And that's been a big part of how we've had to work with the contractor community to get it together is we're like, just do what you've been doing, but look like a Hercules in the field, because it's a quarter, it's a quarter of the weight.
And so they love that.
[00:10:09] Seth: why would we want to use GFRP versus steel?
[00:10:14] Aaron Fisher: Yeah, this is my favorite. I have a, I used to have a, I have a 4 point plan on this as to why we need to use this.
[00:10:20] Seth: You sound like a politician, Aaron. I got
a 4 point plan.
[00:10:24] Aaron Fisher: I actually have a 5 point plan. I don't really need the 5th point. I was joking about this. If I haven't convinced you in the first 4, then I'm not doing my job. Okay. But as the day in Washingtonian, if I didn't have a stump speech ready I it's in a blood here. Anyway what you get, there's four big points.
The biggest point is tensile strength. The reason we use reinforcing bar is because of, we need the tensile strength. By switching from steel to GFRP, you go to a material that has two to three times the tensile strength. That's big. So, alright now we've gotten that performance question out of the way.
So it's stronger, it is lighter. So there's a lot of things that weight plays into. Obviously, most obvious is labor. If you're going to carry a bar from A to B, or go up 2 or 3 flights of stairs, if you're carrying 4 times as many bars. Just because they weigh the same, you're more productive.
And there's very little you can do with labor. Like, we can't turn labor back into slaves. Like, this is not how we're going. Labor rate, labor is getting more expensive. They're, we're not going to be more productive, but you can have them do the same amount of thing, but accomplish more in that same time.
Or conversely, you can think about your cranes on a job site. A big tower crane, how fast that moves limits how much material can get moved. And so now the crane is limited by weight, not by anything else more often than not. And if you can put more material per trip, it's now better. Same thing with hauling and things like that.
So lighter has a lot of things like that. I get into the structural side as well. There's benefits in terms of dead load if your floor is way less. Your footers now need to carry less weight. Your footings or pilings now can be thinner. All things like that. Corrosion. This has probably been the biggest point.
Ultimately, concrete will last for a very long time. Roman concrete. We're all sitting there trying to figure out latest every 6 months. There's a publication. We figured out the secrets of Roman concrete. The secret to Roman concrete is they did not use steel in it. Putting steel in concrete is like giving steel, is like putting a time bomb inside your concrete.
It's not a matter of if it will fail because of the concrete, because of the steel, because the concrete is going to keep pulling in water, and as the water gets to the steel, the iron elements react, and they want to rust. And as soon as they start rusting, they expand, they fall. All the issues that we've seen, it's not a question of if it will happen.
It's when and certainly galvanized stainless steel, epoxy coating that delays that process, but does not stop the process. How do you stop the process? You don't put iron in there to start. You don't put iron. You don't put your steel and that's where an alternative material like G. F. R. P. really has a big win.
Sustainability. This is a really big one. Yeah. Concrete has been, I will say, unfairly the focus of a lot of a lot of the sustainability community. And I say, this is a true, unadulterated sustainability person. And I think a lot of it's being unfortunately driven by the lumber industry.
They say trees are green. The more trees we use, the better, and if we can use lumber in places like mass timber or LVL in place of concrete. They're gunning for the concrete structures and so they've been arguing that more would we use the more sustainable we get. And so they've talked about CO2 emissions.
They played fast and loose and I can go into a lot more detail about that. But in reality, they focused the environmental and sustainability community on cement and concrete. And it's, I've seen the numbers, they're only about 10 percent better than us. When they choose the numbers, so I'm sure what you've I've listed a few staff where you've had a few folks on like the explain how to get 10 percent better concrete.
We can do that, but we haven't really talked about steel on a pert on a weight basis while about a ton of a ton of concrete gives about 3 to 400 pounds of CO2 a ton of steel gives about a ton of CO2 for like rebar. It's even worse for channel beams and things like that. Well, if you use those 2 materials together, you're using concrete, has its CO2 issues and then you're using steel, which has even more CO2 issues.
That's a problem. But by switching to a material like fiberglass rebar, you can actually reduce. The impact of the reinforcing bar by 93%, you can reduce your carbon emissions by that. And so sustainability. Is a big thing is driving a lot of conversation with owners is driving a lot of conversation from the government from state agencies.
They want more sustainable. They want lower embodied carbon and I'm here to present that. And so that's the 4 point play. I talk through strength. I talked through weight. I talked through longevity, and I can an environmental performance, particularly around corrosion. There's a lot more to go there.
And then I specifically talked about sustainability. Now, the 5th point, you're always like, all right, this guy's talking about a great product. It's going to cost me more money. It doesn't. And this has been really the game changer recently where manufacturers have been able to get in that scale up curve.
And I'm pointing down because as you scale up, things get cheaper or get lower cost. Cheaper is the wrong word. I know it's not. The product is not decreased in quality. The product's quality is only getting better, but in increasing production volumes and getting these machines to run 24 7 and do everything you need and automating.
They've actually pulled the cost down pretty dramatically. Where, I'll give you we're a distributor. We sell like you walk in and you're a contractor all day. I'll give you a stick of number four for 6, a 20 foot stick. Now for reference in the DC market, I know everything's a little bit different in some markets.
We only stock domestic steel, but that same steel bar that we sell is like 10. So you're seeing a difference. Like, looking at all things being equal of 40 percent savings and when you talk to a contractor, you say, hey, you're going to buy us every day, but I can save you 40 percent on that.
We've had a lot of contractors walk in. They go. Why is that? What is this? I explained it to me. We go through exactly that kind of 5 point plan. Well, they're convinced on the money 1, the other 4 and they go. Let me try it and then they and what we've seen is contractors once they get in their hands and use it a lot of this stuff.
Like, I'm underselling it, or they weren't listening as well. But needless to say, they're hooked. They love it and they stick with it. And so, and it's not just us. So you can walk into Home Depot and Lowe's and buy a bar there. They put it right next to their steel aisle if you're looking there, they don't have quite the explanation.
Like, they have 1 kind of pop up panel there to explain what the product is. And certainly people are may not be taking full advantage of it or fully understanding what they're doing. But generally, if you're in Home Depot, you're not exactly building high rises. So we're okay there. With what they're doing.
[00:17:21] Seth: I like most of your four point plan. There's a co there's a one or two in there. I could do without, but so if, okay, so you're saying that tensile strength is two to three times of steel rebar. It's lighter than steel rebar. It won't corrode like steel rebar.
And it sounds like the cost is relatively it's more let's can we use the word of it's more efficient as far as the way you'd use it? But so if those 4 things, let's say those are all true. All right. So why is it, why are we not seeing it more out there? I look at, I don't know, a dozen jobs every week.
I go through drawings looking for new work for us. And I can tell you, I haven't seen fiberglass rebar in the drawings yet or specified yet. So what's holding it up?
[00:18:17] Aaron Fisher: Great question, Seth. That is education is probably the biggest thing that's holding up a product like this because.
Until recently, cost was probably one of the bigger ones, but if you're going to look at construction, particularly commercial construction specs drive everything, it needs to be in the codes. Engineers need to reference a code. The building code for the local building code has to reference it. And so what has changed recently has been ACI has published a number of codes.
There's a lot of international codes. IBS is now adopted. So the specific code that's probably the biggest one. ACI 440 1122, which was published Labor Day 2022 was like, the 1st code that said, here's how you do commercial design. It is it has the 440 committees been referenced by ACI 318, which is commercial concrete construction for years at the start of the reinforcing chapter, but nobody pays attention.
Like, they're not looking at the small font. It said, if you want to ACI 440. ACI 440. ACI 440 had been reports since the early 2000s. They design guys beginning like 2010s and it's now a code. So, and then I be the IBC 2024 has now adopted ACI 440 1122 as a code by reference. So, as. Code starts refreshing.
We're starting to see this, but as you probably know, looking through your specs, engineers like to copy and paste their codes, like you're looking at specs for details and codes and things like that for stuff we haven't done for 20 years. So it's a lot of education where you bring this up to engineers and you go, I know the pressure you're under from the owner.
The owner's asking to get costs down. Okay, there's not much you can do. Like, it's not like we're putting gold plated toilets and we're like, all right, we're going to substitute our goal for porcelain. Like, it, there's not a lot of extra money running around in places in a budget. And so, so, so we've been able to get into projects at the 11th hour.
We basically flip an engineering drawing. We work with the engineer. We show them like, things like as concrete in their software. They just aren't clicking all the buttons, like, you're not looking for buttons that you didn't know were there. And so you can click a button and say, I want to design my rebar and detailing not to traditional, but I want to design it to GFRP CI-440.11 and use the relevant codes and. It just does all the calculations for you, and you watch the engineers like lights go on and go. Oh, I thought you were going to make me do like, pull out a pen and paper and some slide rules here. And I'm like no, like, it's in the codes. It's in the software.
Now that the codes that basically most engineers use, they just aren't clicking. And so. We've been able to do a lot of this and DOTs are a whole different ball game. I've left them aside, but the DOTs understand the true cost of corrosion. Like, if you're looking at bridges or seawalls or things like our pavement structures.
The you deal with the structure even that we were discussing snow beforehand, even in Richmond, like if it snows, you're throwing down a lot of salt. , you, I'm sure you've talked a lot about what salt does to concrete and particularly to the rebar. Well, the jurisdictions now under are understanding this.
They have a rough number of what they do in maintenance, and you look at them and they go, oh, so about 20 years ago they looked at this product and they said this could be a big deal. And they actually built some bridges. There's actually a bridge. Actually in welcome to, I, we're going to play a little geography here, but I'm sorry for anyone who's international or not in the Virginia area, but outside of Roanoke, there's a place called Smith Mountain Lake.
There is a bridge over Smith Mountain Lake that was built about 20 years ago with GFRP in it. This was not the 3rd generation of bars. This is much of the early stuff, but you haven't heard about it. I haven't, I nobody's heard about it because it's still standing. It's working like a bridge.
And that's the key thing, but to reinforce this, a lot of these bridges that were built were curiosity. So we've come back and done like core samples. Like, all right, how long is this? What is the quality of the rebar on this bridge? And they actually went and did this about 15 years after this was Dr.
Nani's work with along with a couple of other folks. So it's not just him. He's not out there. I don't know if he's the one out there operating the core driller, but they basically looked at these samples and they said, are these bridges are 15 years old. They'll go another, they'll go 102 years plus, 100 years plus, and you go before a major rehab, before a major repair, and that's what these DOTs saw they're, they've understood this, so Florida's actually been doing it as a DOT for about 10 years, Ohio's been doing it for 5, and like, as, like, they've started to fall like dominoes, because South Carolina, North Carolina, Virginia, I know Maryland's about to drop something, you go up to Maine, and you just go down and like, Texas has it.
Like, you're like, these states don't agree on anything. Oh, Michigan. Like, these states agree on nothing, but they agree that corrosion costs them too much money in their DOTs. And that has been this big shift where they, and so AASHTO has bridge design guides and things like this as well to drive that side of the community.
But again it's an education piece. Like, I joke with engineers all the time and, or they'll tell me like, Okay. Look, if you're driving on a bridge in Maryland and a bomb happened to hit it, the bridge would still be standing after the bomb. Now, shrapnel, I'm not going to go on what the shrapnel might do to you, but the bridge will still stand.
And they go, we have over engineered bridges for 40 years, but we haven't touched the spec in 40 years. Like, it is, and that's been the challenge is that we're trying to update specs, get new materials in. The most common, when I go to talk to someone at a DOT or a state agency, they're like, why would anybody want to do this?
It's like. I need a project in front of me, but I go to an engineer and they go, I'm not going to spend my time engineering this unless it's in the codes already. And then the contractor goes, we're not going to propose this unless the engineer and the regulator, and it bless this. And what's funny is you get all 3 of them in the same room and they go, nobody has an actual objection to this material.
And that's what we're starting to see a shift is there's people who are able to pull those 3 groups together. And then and move the needle and that's where we're starting to see a lot of projects move very quickly that are very public. You go down it and it's just it's stunning how quickly this is done.
Virginia VDOT, which does not have a standard has actually snuck it into. The harbor tunnel projects under design built. So design build, obviously, you're not exactly having to follow the state specs. You have a little bit more latitude because the engineer and the contractor are working so closely together.
They are able to make the case by themselves without the regulator, but to the level of confidence that they can take the engineering the level of confidence and they can actually do that, and they can actually incorporate it into those structures. So we see FRP down there and that's what we're seeing is it's just sneaking in a lot of places and now.
We're seeing that people are like, oh yeah, we need to formalize this. And so that's where a lot of the ASHTO design guide, the ACI has come along. TMS, the masonry society has come along and everybody's putting these codes together and they're starting to make sense, but the field is rapidly changing in front of us which is both good and scary, but needless to say, I think the biggest thing I can get to your audience is if you took a steel.
If you designed a bridge with steel, you can pretty much. Up into the 11th hour, convert that bridge over to and it would function the same way cost and a material basis is roughly going to be pretty close. So, on a commercial job, you're buying much more direct. From a male, like, there's a lot less markup coming through.
You're pretty close on costs, but what you're really going to save on is maintenance and longevity. You're going to have a bridge that last 100 years doesn't need nearly the same maintenance and as gravy on top. As I mentioned, it's a sustainable material. So, for jurisdictions that are under that kind of decree, it's going green without spending more green.
[00:26:17] Seth: Oh, do you have that trademark?
[00:26:20] Aaron Fisher: I say a lot of things.
[00:26:21] Seth: going green without spending a lot of green. Yeah. Should trademark that, Aaron.
[00:26:27] Aaron Fisher: I'll try to. I'm a reformed sustainability guy. More times I have to argue with people in the sustainability community about what's practical. Right. And I'm like, because I don't care if we have something that's, that, that's purely like the greatest thing to slice bread.
But if it costs too much money and it, no one's gonna do it. There's so that's kind of it. So going green without spending more. I guess I'll trademark. All right, full trademark there. I'll stop arguing. I don't have the trademark and just take it.
[00:26:54] Seth: Just take it. Yeah. So, but when you're doing these conversions and you're getting people on board to use GFRP, you got to explain to them the limitations of it too, right? There's got to be some limitations that you got to be up front with them to tell them, hey, I don't want you to be surprised when you run across this particular condition or this particular building element. GFRP is not the thing.
Is there anything like that, that you let engineers and designers know ahead of time?
[00:27:28] Aaron Fisher: So. Certainly, there are certain things, and I think it has to do with where the code is now. So, engineers like that code is a safe space for engineers. And what does the code say now is you can't design in high seismic, D, E, and F seismic.
Okay, but what can I tell you is Japan has been doing this since the 90s. Everything in Japan is high seismic. So what the challenge is actually, it's a bigger discussion in the seismic community where, and I'm sorry, I'm going to do a little bit of a visual here, but for anyone who's watching, I'm showing like, when a building goes through an earthquake, it moves.
And generally what we rely on is the steel kind of dampens that motion back and forth. Like that. Internationally, that is not how seismic reinforcement is done. They actually have the whole building rock. And then it slows down as one single piece. In that kind of design, because the bond strength between the bar and the concrete is so much higher, it actually holds together.
Now you're not trying to figure out how damaged your bar and your concrete is to each other as you would when it happens like this. That's a bigger discussion. Like, I'm trying to, but. Because the rest of the international community was already pushing this way before we started before came onto the scenes.
We're starting to see the seismic codes reflect that and that's leading to some changes. But if you're using ACI 440.11, I have to tell you, you can't do it with ACI 440, but we know how to the engineering is there. What else I can tell you, if you're looking, if you're a structural precaster. Certainly this is an area that people are looking at, but ACI 440 says.
This code is not talking about structural pre casting, particularly around pre stressing. It does not talk about pre stressing. Why? The material behaves slightly differently. So if you were to bend steel and bend it back, it gets back to where it is, but it doesn't quite come back to where it is.
And so in a stress strain curve, it keeps moving. It has an effect that you've damaged it. Like it remembers the damage. GFRP is actually different. Until it breaks, it goes right back to where it is. So the motion is so there's not a question of, hey, how many times is it bent?
I don't care. Either it's broken or it's not. That's the binary condition we get to. That's truly what a brittle material is. Like, everyone thinks of, like, your grandma's face is brittle. It's truly brittle. Like, if you drop it. We know exactly what's going to happen to your grandma's vase. It's not you're gonna, you're gonna have a really upset grandma.
If you take a bar and drop a bar from the same height down to the ground, it stays together. Like, it's brittle, but the failure point is so far beyond where you expect because of what the resin is imparting. It's imparting those properties to that bar. But the way the code takes care of that is that they take you much further away from that failure point.
And so, why GFRP, well, it might be like 180 KSI. The code only lets you 150 to 180. You can only use about a third of that value if you're stressing it. So, alright, that takes you down to like 50 to 60 KSI. That's equivalent to where you can take your steel, like grade 60, you can stress it to like 80 percent because it yields.
You're in the same ballpark, but that's where a material like carbon fiber reinforced polymer actually comes in, CFRP. It is much more expensive. This is not a, it's, but performance wise, it's tensile strength is like 350 plus. So a third of that, you're over a hundred KSI. Like you can really bend it.
You can really stress it. And you're still nowhere near the failure point. What else could you get into? Let's see other applications that, certainly, those are probably the two biggest ones. As I mentioned at the outset, people do always get worked up that you can't bend it.
But I can tell you as a guy who works with out in the field with folks, like we stock common bends. We like, so you need an elbow, you need to start up like. If we know what's coming, we can do that. Obviously, everything in the factory, the lead time is to get to site for like a big truckload is like two weeks.
If you need like something immediately, as I mentioned, these machines run 24 seven, they just pull it in and they can airship it because it weighs nothing. So like, if you forgot like an exact piece, there's nothing else you can do there. You can do that. But that being said, the way the codes are written, you can lap in with steel.
Like they are very conservative. And detrimental to GFRP in favor of steel, you could lap in with steel, say you needed some bend, and you couldn't get it. And you're like, I could walk over to Home Depot and get it. All right, great. Bend it in with steel. But that being said, you get to like a residential corner and you're used to having those corners there.
You're like, all right, that's great. It's actually stronger to do a 45 degree lap splice. Why, as you might imagine, when you bend glass, it tends to start breaking the glass. So the fiber starts to damage. And so a straight glass bar is actually stronger in the directions that you're interested in. And then once the concrete's in place, the bond is actually not between from the bar to the bend to the other bar.
It's from the bar to the concrete to the other bar. And so the concrete is really the glue. You're just trying to hold it for placement. And that's It requires a lot of conversations. And when I get it, when I get in front of a contractor, who's really understanding this, like, there's a lot we can do.
Like, what we do pretty regularly is a contractor says, oh, I'm used to using number 4s or number 5s of the thing. I go, downsize that number 5 grade beam, all those bars in the grade. You can use number 4. I have details that show that I have a Ryan Holmes detail. I'm in NVR homes. They are, look, I joke all the time, but to their credit, they make affordable housing.
But they are the kind of people that they would sell their grandmother for a nickel. Like, they are very interested, they understand their costs, and they're doing everything they can to drive it down. I've got it in front of them. I've got their drawing flipped. And that's the kind of thing where it's like, and they're looking and they go, alright, I know exactly what it is.
We'll compare bar to bar. If you guys are cheaper on a job, we'll take you. Because you meet code. If Steele's cheaper on a job, we'll take you. And that's really where it is with a lot of this stuff is that, but I'm pricing as number 5 steel. So I have my 6 dollar bar and I'm trying to compete with someone's number 5 steel bar.
I'm at a really good advantage there and that's how we that's how we get a lot of this cost advantages is. You're looking at a big structure number 8, number 7. I can take that number to get number 6 is. That's a big downsizing bars has well, it helps with material. It also helps with placement.
It helps with confinement, congestion, those kind of things. And these are the kind of things you don't think about. And it's really tough to get someone to understand it. But once we get people using it, there's a lot of tips and tricks we can give somebody that makes them they just. Whatever the hook is, we get into you, we can, and then we give you the rest of the store with it.
And they really are sold.
[00:34:19] Seth: Yeah. I think that's a perfect spot for us to stop today. Aaron. If folks want to reach out to you and learn more about GFRP and maybe say, hey, I got this job. Can you flip it from rebar, steel rebar to GFRP? What's the best way of them getting ahold of you?
[00:34:42] Aaron Fisher: Best way to get in touch with me? Email. My, my name is Aaron Fisher. My email, afisher, A F I S H E R. There's no C in case anyone's wondering. At emco, E M C O block dot com. I also, I guess I'll put my phone number if somebody wants to call me. 202-510-5545. If you want to give me a ring I generally answer my work phone at all odds hours.
So I'm happy to be a resource. I'm happy to connect you with folks. I'm not the only person who knows this, but certainly I spent my time to get this up to speed and we're really convinced. We've convinced a lot of folks in the DC area. So big shout out to reliable. Any job they can get their hands on, they're given to us.
And they're like just. Do you guys save money? Like we like it. We save money. We save money on material. We save money on labor. And then ultimately, we're winning more jobs because it's just cost effective. And that's really the thing. If you're struggling on costs, you're not winning some bids, give us a call.
Hopefully we got a solution for you.
[00:35:37] Seth: it's a cool technology and definitely something for folks to look into. All right, Aaron, I appreciate you coming on the show today. Folks until next time, let's keep it concrete.
VP of Business Development
Dr. Aaron Fisher has a PhD in Chemical Engineering from the University of Maryland and a B.S. in Chemistry from Duke University. He is currently the Vice President of Business Development for Ernest Maier; a family-owned company. Dr. Fisher is responsible for PaveDrain a heavy duty, low-maintenance permeable pavement and fiberglass rebar, a stronger, more sustainable, corrosion-proof alternative to steel rebar. Dr. Fisher has a deep technical background in all aspects of sustainability. He has served as a contractor to several programmatic offices within the U.S. Department of Energy- Energy Efficiency and Renewable Energy Office. He has also led the innovation program at Water Research Foundation on behalf of wastewater, stormwater, and drinking water utilities across the United States.