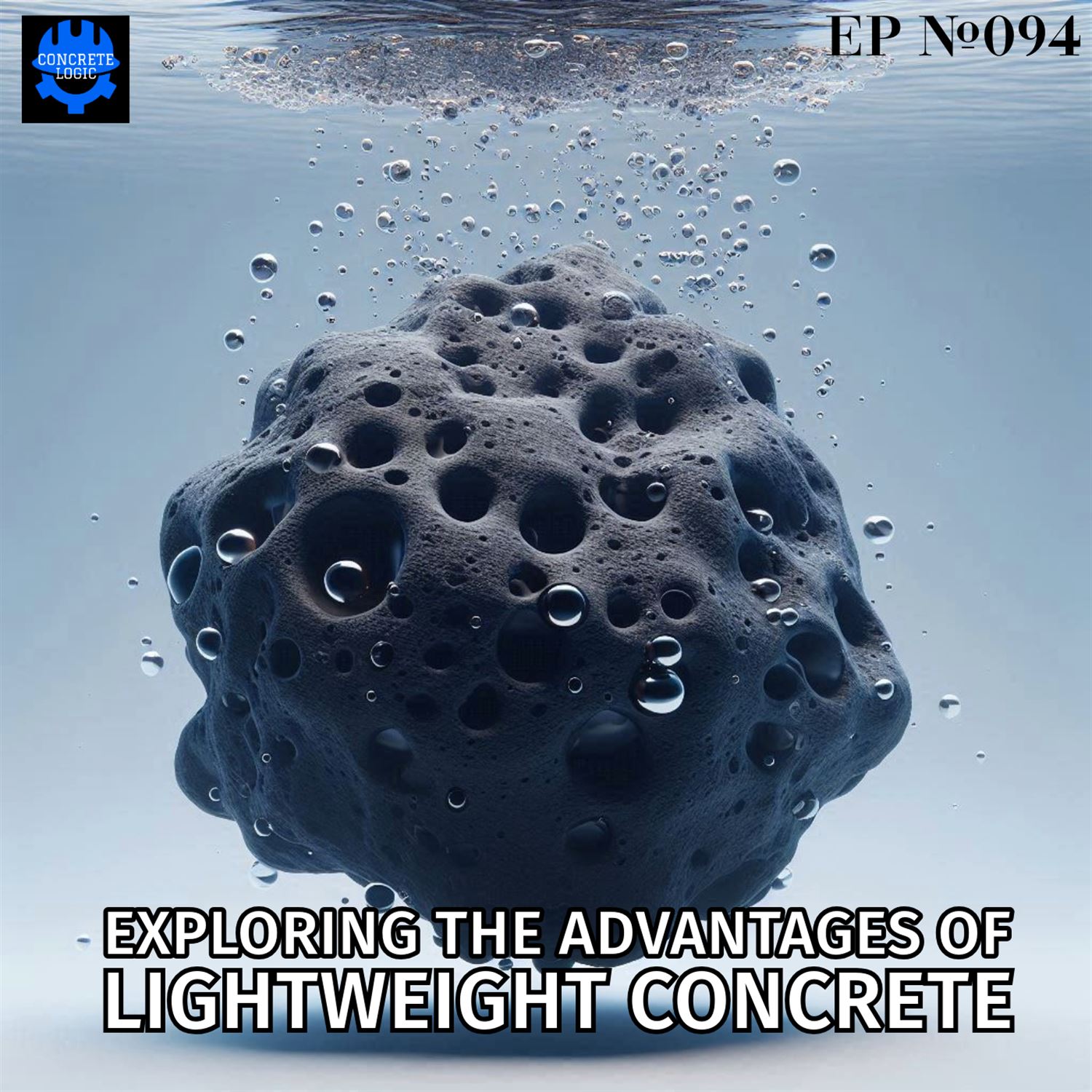
In this episode of the Concrete Logic podcast, Seth interviews Kevin Cavanaugh from Arcosa Lightweight Aggregates about lightweight concrete. They discuss the history and types of lightweight aggregates, the advantages of using lightweight concrete, and the special considerations for handling and finishing lightweight concrete. They also touch on the use of lightweight concrete in response to the challenges of Type 1L cement. Overall, the conversation highlights the benefits and misconceptions surrounding lightweight concrete.
Takeaways
Chapters
00:00 Introduction and Overview
04:19 Types and History of Lightweight Aggregates
09:03 Advantages of Lightweight Concrete
12:40 Special Considerations for Handling and Finishing Lightweight Concrete
18:03 Using Lightweight Concrete for Type 1L Cement Challenges
33:44 Dispelling Misconceptions about Lightweight Concrete
38:00 Conclusion
Did you learn something from this episode? If so, please consider donating to the show to help us continue to provide high-quality content for the concrete industry. Donate here: https://www.concretelogicpodcast.com/support/
Episode References
Guest: Kevin Cavanaugh | Arcosa Lightweight Aggregates | kevin.cavanaugh@arcosa.com
Guest Website: https://arcosalightweight.com/
Producers: Jodi Tandett
Donate & Become a Producer: https://www.concretelogicpodcast.com/support/
Music: Mike Dunton | https://www.mikeduntonmusic.com | mikeduntonmusic@gmail.com | Instagram @Mike_Dunton
Host: Seth Tandett, seth@concretelogicpodcast.com
Host LinkedIn: https://www.linkedin.com/in/seth-tandett/
Website: https://www.concretelogicpodcast.com/
LinkedIn: https://www.linkedin.com/company/concrete-logic-podcast
00:00 - Introduction and Overview
04:19 - Types and History of Lightweight Aggregates
09:03 - Advantages of Lightweight Concrete
12:40 - Special Considerations for Handling and Finishing Lightweight Concrete
18:03 - Using Lightweight Concrete for Type 1L Cement Challenges
33:44 - Dispelling Misconceptions about Lightweight Concrete
38:00 - Conclusion Did you learn something from this episode? If so, please consider donating to the show…
Seth (00:03.771)
Welcome to another episode of the concrete logic podcast. And today I have Kevin Cavanaugh with our COSA lightweight. Did I get it? Hey, Kevin, I say your name, right? All right. Off to a good start, Kevin. before we get into the topic today, which is, lightweight aggregates, and, we're going to talk about how they, obviously lightweight concrete, this concrete show. So we're going to talk about concrete obviously, but Kevin also
Kevin Cavanaugh (00:14.22)
That's correct. Yes, sir.
Seth (00:33.979)
deals with, CMU, lightweight CMU. So, we may talk a little bit about that as well, but before we get started, just to remind everybody, the three things that you can do for me, if you listen to this podcast, I need your help, to, you can support the show and three ways. The first way is share the podcast, share it with somebody, you know, somebody doesn't listen, maybe somebody that does listen and you, and they, maybe they didn't listen to the episode and
You said, Hey, this was a great episode. Make sure you listen to this one. but please make sure you're sharing it. the second thing you can do is if you go to concrete logic podcast .com, there are a couple of ways that you can reach out to me. there's a contact, button at the top and I'm going over there right now. Yeah. It says contact. so click on contact and you can shoot me a message.
And what I'm looking for there is a topic or guest suggestion for the show. A majority of the shows that we have are suggestions from either folks that are listening to the show or past guests. So those, you know, those suggestions are very helpful. That way we are putting out episodes that you actually want to hear. You can also, if you...
would like, you can leave me a voicemail too. If you're like me, if you like to talk versus writing, I rather talk. That's why I do a podcast. I feel like I'm better at this than I am at the writing part. But anyways, there's a, there's a microphone in the bottom right hand corner. You click on that and it re it records your voice right over your computer. And it leaves me a voicemail. and again, just, that's another way you can give me a idea for a guest or a topic.
And if you want, when you leave the message, we've had this happen before where someone said, Hey, you can play my message on the podcast. so we can do that too, if you'd like. So, and then the last way is in the upper right -hand corner of the, of the homepage on the, website, concrete logic podcast .com. There's a donate button. If you, click on that donate button.
Seth (02:57.307)
you get a couple of options on how you can donate to the show. There's a monthly subscription thing. there's a, a wave there. You can leave any amount and that's just a way of you, showing that you're listening to show you appreciate the show because we don't charge you for what we put out. We give it to you for free. And then you come back and you tell me what it was worth to you. So it's called a value for value model.
So there's no paywalls or anything like that, which is very annoying to me, especially on LinkedIn, when someone posts something and they'd say, Hey, check this out and you click on it. And then there's a paywall. That's really annoying. We don't have paywalls on concrete logic podcasts. So. Yeah. So we put out like today, Kevin's going to share his wisdom with us today. And then you can come back and say, Hey, this, this was how much it was worth. And you can, any amount, any amount.
you can, you give is, is appreciated. So, okay. With that, Kevin, so Kevin, is with our COSA lightweight aggregates. I guess you probably should start with what the heck is a lightweight aggregates and why do concrete folks, care about it or should care about it.
Kevin Cavanaugh (04:19.404)
First of all, there are many different types of lightweight aggregates. There's natural, volcanic, scoria, pumice, that type of material. From volcanic activity, it's been used for on and on centuries, actually, starting with the Romans, Parthenon, one of the largest, if not still the largest, unsupported dome on the planet. That was volcanic material 2 ,000 years ago.
Modern light wet aggregates, the type that are used in most concrete applications, other than insulating, there are insulating concrete materials, pearlite, vermiculite. There's cellular concretes. It's a lot of air entrained additives to give a very bread, analogy to a slice of bread. There's a lot of air bubbles in there. But the materials that we deal with are structural grade, ceramic.
aggregates made in a rotary kiln. The kiln is not the same size and it doesn't burn as high a temperature as a cement kiln, but otherwise it's very similar. I am not a manufacturing expert. I couldn't even tell you how long it takes the material to traverse through the kiln. I'm going to guess it's 25 minutes, something like that maybe. But the modern light wood aggregates
was actually an accidental discovery about 100 years ago, maybe 107 years ago in 1917, roughly. Clay brick manufacturer in the middle part of the country in Kansas, Stephen Haidt, H -A -Y -D -E, noticed that his clay brick were coming out of his, I don't know what type of, how he fired them, but his end products were having little...
little balls and little knobs of material that was ruining the rectangular prism shape of the clay brick. So he did a little more research. He tinkered and he just, you know, some folks have said given lemons make lemonade. So he refined what was happening in the kiln. He studied it and lo and behold, he found a valuable material, ceramic, structural grade, light wood aggregates.
Kevin Cavanaugh (06:40.396)
And these are made from either shales, clays, or slate. They all have very similar chemical and mineralogical characteristics. As you can imagine, slate is denser and harder. We sometimes use it in roof shingles. And then you have shale, which is a little bit softer. And then you have clay. And it's really a matter of how long that material's been in the ground and under pressure for however long that deposit's been there. But when they're heated,
They all bloat to a degree. This is what was happening to Stephen Hayes Clay in the Clay Brick. And he patented this and he received a patent from the, he applied for a patent and received a patent from the federal government and promptly gave that patent to the US government so they could make ships for World War I. There was a shortage of steel. And some of those ships are still,
in existence today, one of them is the USS Selma. It's in Galveston Bay, Texas. It's in a saltwater environment. It serves as a lab where gurus and concrete folks like us can go out and take core samples and look at the condition of the concrete. And then there's another one up on the Powell River in British Columbia that I'm not sure. One of my colleagues actually did a Google search.
recently, but still may serve as a dock of some sort or a platform for industry. What's interesting is these concretes. Sure.
Seth (08:15.419)
And then I was going to give you a little breather here there. the, and then they have the ones that they're there, obviously at a commission, but up on the Eastern shore in Virginia, there's a graveyard of the, of the other ones that they built, which I didn't know till. Yeah.
Kevin Cavanaugh (08:34.54)
I think they're from the same timeframe. Yeah, and I think there are also some in just north of the big bridge on the south side of the Beltway in Washington, D .C. I grew up in D .C. area, and there are some sunk in there as well on purpose. Yeah, yeah. No, that's fine. But so these ships serve as a way to look at the
Seth (08:53.243)
Yeah, cool. Sorry to interrupt you. Keep going.
Kevin Cavanaugh (09:03.916)
durability of lightweight concrete over time. And you have to keep in mind these ships were all lightweight material, lightweight fines and coarse, lightweight cement, water, et cetera. Today, we typically, it's all coarse aggregate and sand. Whereas, and that changed and roughly then I want to say like the 1970s when the oil embargoes caused the price of fuel to rise. So to make the concrete more
economical, we removed one of the ingredients of the lightweight component, the sand, and it's basically coarse aggregate today. But what we discovered, well, I got to piece together certain different pieces, but the interesting thing is we all know that concrete hydrates forever. Some of these ships, the Powell River ship, it's like 105 pound per cubic foot material. It's like 9 ,000 psi today, one of the core samples that I
was privy to seeing the data on it. And it was initially 5 ,000 PSI, the mix design. So these ships, and I have a sample of a bridge actually in Richmond, Virginia. I don't know whether that's upside down or not right here. That's the company I used to work for. This was the wearing surface of the nickel bridge, which was replaced in...
Seth (10:27.867)
yeah!
Kevin Cavanaugh (10:31.852)
It was built in 1959 and it was replaced when I lived in Richmond and worked for a Lightwood aggregate company that was based there.
Seth (10:37.371)
You won't, you won't believe this. I lived like two miles from that bridge.
Kevin Cavanaugh (10:43.724)
Yeah, so there's not a lot of cover over this piece of rebar. And this was actually coated with like a varnish. But the rust you see there is from being exposed to the air. It's not from the penetration of any chlorides or bad materials. But the ships gave insight because they're all lightweight materials. And going back about
30 years ago when all the supplementary cementitious materials came into being used more and more, especially for bridge decks, we wanted to make them very impermeable. We learned that we made them very strong and somewhat brittle and we had cracking issues occurring, drying shrinkage cracking, as well as chemical shrinkage because we couldn't get enough water to the supplementary cementitious materials.
What we learned from these old samples of concrete from the ships is there's another mechanism occurring and it goes back to some research in the 50s and 60s. It was internal curing. The lightweight fines distributed throughout the paste in the matrix are small bubbles, if you will, or small sponges that have water that can be available for long -term hydration.
So I know I've kind of covered a lot of different territory in the history of modern lightweight aggregate. It was an accidental discovery by the clay brick maker. And then it started to be used in concrete chips because of shortage of steel. And then why you use lightweight concrete as a high strength to weight ratio, frankly.
Kevin Cavanaugh (12:35.98)
I'll give you a chance to maybe absorb some of that and ask me a question because I did.
Seth (12:40.027)
Yeah, could you maybe compare a standard weight, normal weight concrete? Like if you were to take a, I guess compare the, maybe the, I don't want to say specific density, that's going to, maybe people don't have our time. If you were to do like a normal slab, like an eight inch slab.
Could you compare the weight for a lightweight concrete versus a normal weight concrete or something? Give us kind of a comparison there so we understand why we use lightweight concrete.
Kevin Cavanaugh (13:15.724)
Well, yeah, the density of the concrete at equilibrium for light weights anywhere between 105 to 120. Common ones are 110 and 115. That's at equilibrium. Whereas normal weight concrete is 145, 140. And so depending on which of those two you're using as the basis, if you're going from
the lightweight to the heavyweight. Now that's 30 pounds extra over 105, 110. That's about 30 % more weight. If you go the other way, it's about, it's lighter. 30 divided by 145, it's 20%. Depends which you're using as your basis of comparison.
Seth (14:08.891)
Right. And we would use lightweight concrete because it'd make the overall structure lighter. So therefore, your foundations could be less substantial compared to a normal weight structure. So there's savings there. Am I going down the right path? What other advantages are there to use in lightweight concrete versus normal weight?
Kevin Cavanaugh (14:33.932)
Well, the weight is one of them for sure. I mean, you can use smaller steel columns or fewer beams in a building. That's the case of a recently finished project in Chicago, Salesforce Tower. And I believe that was one of the winners of ACI competition and it's gonna be presented by the contractor that did the work.
That's it.
Kevin Cavanaugh (15:02.412)
at the ACI convention in the fall. And right now the name of the contractor is failing me, but I could pull up the case study. But that's number one, you know, the weight reduction allows to less steel. And today with the focus on carbons, reducing the amount of carbon and body carbon in materials. If you have less steel in the building, that's a good thing. If you have lightweight concrete, it allows you to do that.
Now this is a high rise building, it was 58 stories. And if it had been normal weight concrete, they would have had to have multiple extra picks of the crane to pick up mostly the beams, or they would have had smaller bay sizes. So there would have been more steel and more picks of the crane.
Kevin Cavanaugh (15:54.348)
it actually allowed the job to be completed quicker.
Seth (16:00.955)
You know.
Kevin Cavanaugh (16:01.58)
So that...
Now go ahead.
Seth (16:04.987)
And you're not using, you don't use sand in the lightweight concrete mixes. Did I hear that right?
Kevin Cavanaugh (16:09.644)
we don't use we don't use the lightweight fines the light weights and you do use pardon me that's the landline you do use natural sand natural fines course lightweight aggregate
Seth (16:26.843)
Okay. And.
Kevin Cavanaugh (16:28.556)
The other big reason in high -rise steel frame metal deck, and this could be a steel frame metal deck building that's two or three stories, is the fire ratings. If you have a corrugated metal deck, you put lightweight concrete on it, it's three and a quarter inches, I believe, versus four and a half for normal weight concrete to have the two hour fire rating. And with a lightweight deck, you actually don't even have to put fireproofing spray underneath.
on the ceiling side of the floor below. You do have the fireproofing spray in both of these applications on the columns and the beams. But in the case of the lightweight system, you don't have to put it on the bottom side of the corrugated deck. It's a UL fire rating.
So that would be probably the big two is you have better fire resistance, less concrete to be used to get that same hourly fire rating, which then allows you to have thinner slabs, which once again helps reduce the amount of steel that's in the building.
Seth (17:44.539)
OK. All right. So those are the benefits. Are there any downsides to using lightweight concrete? I mean, should it be used for every type of job, or is there some jobs where it doesn't make sense to use lightweight concrete?
Kevin Cavanaugh (18:03.916)
Well, you're talking to a lightweight concrete guy here. So, but no.
Seth (18:08.091)
I was selling, but I mean, I mean, we, you know, as a, as a expert in, in lightweight concrete or expert in anything, I think customers appreciate where you, you tell them, Hey, you know, the, this is not an ideal project versus, trying to sell them. I'm the same way. I, I just told an engineer the other day that he shouldn't have, he shouldn't have designed a steel building. It should have been concrete and I'm sure he appreciated that comment, but,
Kevin Cavanaugh (18:28.044)
Yeah, well
Seth (18:39.195)
I mean, what are the downsides? I know I have a little bit of experience with lightweight concrete. So one of the things I can think of, and I'm on your Arcoso website, and I'm just reminding myself of some of the nuances of lightweight concrete. And one of them is the special handling of the aggregate. What do you have to make sure to do with the aggregate?
Kevin Cavanaugh (18:45.356)
I can give you a couple.
Kevin Cavanaugh (19:08.364)
you need to pre -soak the light wood aggregate, especially if you're going to pump it. We have rec and, go ahead.
Seth (19:09.371)
versus normal weight concrete.
Seth (19:15.131)
Yeah. Right. Yeah. I did a job in.
I did a job in Cleveland and we couldn't figure out why we couldn't pump the lightweight concrete. And I ended up being the guy that went out there and make sure they were soaking the aggregate, before it came out to the site. no. this is early in my career, long, long time ago. but, so you gotta make sure you're soaking the soaking the aggregate. Is that just for
Kevin Cavanaugh (19:34.188)
Was this recent? Was this recently?
Seth (19:49.339)
pumping considerations or is that just good practice overall?
Kevin Cavanaugh (19:54.732)
It's probably good practice, but it's not necessary to make concrete. If you don't pre -soak, you're not going to get any type of internal curing from the fines or the coarse material. And again, I didn't explain the internal curing all that much in detail, but you use fines in internal curing because you have more distribution of reservoirs of water versus the larger sizes, the coarse aggregate.
Kevin Cavanaugh (20:24.044)
You definitely want to get the material to SSD, saturated surface dry. Earlier in my career that was flipped around the other way, so I might be saying it backwards, surface dry, saturated. But you can do it with typical garden sprinkler, you know, it's just an oscillating spray head and turn the pile. And if you're going to pump, probably good practice would be to turn the sprinklers off the night before to let the pile reach an equilibrium.
and then maybe fold the pile the morning of so you don't have pockets that are real wet or pockets that are dry, then you can confirm this by taking a unit weight measurement the morning of the pour. You know what it's supposed to be damp, loose, and you know what it's supposed to be in a dry state. If the aggregate production is consistent, you know those two numbers.
You can adjust the batch actually if you have, if the material is supposed to be 50 pounds a cubic foot and you measure it at 45, there's not enough moisture in there, but you can still batch it, you can still place it. If you're going to pump it, you may have a bit of a problem, but you want it to be at SSD, saturated surface dry. And that's typically depending on the aggregates and there's
Multiple producers in the US have expanded shale clays and slates. We all have the similar characteristic where it very quickly in the first half an hour, hour or two, it spikes as it absorbs moisture and then it kind of levels off over time. The final absorption could be anywhere from six, seven, eight percent up to around 30 percent depending on the aggregate type.
But those curves, they all match one another. The shape of those curves is, they're identical pretty much with manufactured expanded shells, clays and slates.
Seth (22:25.179)
You're saying this, the saturation, the lightweight, saturating the water when you're soaking it. Is that what you're saying?
Kevin Cavanaugh (22:33.612)
Yeah, when you're sprinkling it to... See, we use the term pre -soak, but it's really... You're not necessarily dumping it into a pit of water. You're going to trap air underneath the aggregate. When you dump it in, it's better to do the reverse where you put it in a pool and then you fill that pool up with water. So the water rises up around it. In the Northern climates, a lot of producers do that, Chicago, Minneapolis. They call them soaking pits. And then...
Seth (23:00.251)
okay.
Kevin Cavanaugh (23:01.452)
where it's, you know, extreme cold up here around in the Great Lakes area where I'm, I live in Milwaukee. You can condition the material before winter sets in and it'll keep that moisture and you can do projects in the, in the middle of winter. If you're not typically doing a lot of lightweight concrete, it can be a challenge for some ready -mix producers that don't do it regularly because it's difficult to do that outdoors.
You definitely can't sprinkle when it's sub -freezing temperatures.
Seth (23:34.299)
Right. Yeah. Usually you see sprinklers out. That's what I've seen before. I didn't know they dipped them in vats. Huh?
Kevin Cavanaugh (23:41.068)
Yeah, that's pretty typical.
Kevin Cavanaugh (23:45.932)
It's like the size of a swimming pool, depending on the size of the operation the ReadyMix producer.
Seth (23:52.283)
What about, so that's the internal carrying that you're referencing is that you're, you're soaking the aggregate before, and then the aggregate is slowly releasing the water and, and doing so it's internally carrying the concrete.
Kevin Cavanaugh (24:13.388)
Yes, exactly. So I didn't fully explain how we got to internal curing in the last couple of decades, but it had to do with the bridge deck concrete with the very low permeabilities that were achieved in the lab with the supplementary cementitious materials. But in the field, we were experiencing a lot of cracking in these bridge decks. So we're kind of defeating ourselves.
So in order to hydrate that SCMs in there, you had to have an extra source of moisture, which in this case is brought to the concrete by the light wood aggregate defines. It distributes the water more effectively. A lot of research done. There's an equation that a gentleman at the Bureau of Standards. When I was in college, I was a co -op student in the heat transfer into this lab, and he was down on the concrete. And what is called the Bents equation, B -E -N -T -Z.
and it's 7 % by weight of the cement or the cementitious materials, that's the amount of moisture you need to have absorbed within the light wet aggregate. Or you have to have that amount of water available and that water is brought into the concrete via the light wet aggregate. So if it's a mix with, let's do simple math, if it's a
If I could do this off the top of my head, 500 pounds of cement, 7 % of that is 35 pounds of water that you want to have in the aggregate itself. And if you know the water, the aggregate absorbs 10%, you can figure out how many cubic feet, 10%, how many cubic feet of lightweight aggregate you have to have. And it's typically, with the materials that I'm familiar with, it's two or three cubic feet of material.
There are some places, the state of New York that just said, hey, and what you do with that two or three cubic feet of material is you take out the natural sand that's not absorptive, doesn't have water absorbed into it, it has surface water, you replace it with a lightweight fines. The state of New York said, let's just make this simple because we don't want people to go through the math and just replace, I think it's 30 % of the natural sand with lightweight fines. And that covers most of the mixes. Yeah.
Seth (26:40.891)
Do you, do you, do you find when they use lightweight concrete or are they still, carrying externally or no.
Kevin Cavanaugh (26:50.284)
We have never recommended to eliminate external curing. Some researchers are leaning that direction. I'm not on top of all the most recent research, like some of my colleagues that attend the ACI 213 committee meetings and the 308 pavements, but some are moving that direction. There are also some products in the market that call themselves internal cure, but it's not lightweight.
expanded shell, claser, slates, that's doing it. It's sort of a...
It's a good name they selected, but I don't know that everyone agrees it's internal curing what's happening.
Seth (27:34.459)
You're referring to colloidal silica products?
Kevin Cavanaugh (27:37.804)
Yeah, yeah. I understand they don't give up the water because of an electrical charge. And depending on how fine that colloidal silica particle is, sometimes they refer to it as liquid fly ash and then other times they call it internal cure, depending on the size of those particles. And I know they've had good performance. I don't want to smudge the good performance they've had.
Seth (27:55.995)
Right.
Kevin Cavanaugh (28:06.412)
It's slightly different, I believe, from the way internal curing happens as we understand it.
Seth (28:12.283)
Yeah, I mean, it's different from what you're talking about.
Huh. Yeah, I didn't, I didn't, when you, when I saw your note about internal carrying, I thought you were going to go somewhere else with it. So I,
Kevin Cavanaugh (28:19.468)
But you
Kevin Cavanaugh (28:29.772)
Where did you think that I was going to take that?
Seth (28:30.011)
Yeah, that makes sense.
I don't know. I saw your note. I was like, because we've had the internal curing folks on here. And we've talked about colloidal silica numerous times. And like you said, they've had great success with it. It seems to be a
Kevin Cavanaugh (28:34.956)
okay.
Seth (28:52.411)
It seems to be one of the remedies out there to deal with the new fin angle type 1L cement. Since that cement seems to be water starved, so it's another source for that cement, it seems like. Have you seen, I know you're not totally well versed in everything going on with the concrete side, but have you seen any?
I guess here's a question for you. Since the type 1L transition has, have you seen an increase in use of lightweight concrete?
Kevin Cavanaugh (29:33.74)
I wouldn't say so, no. I mean, I think mostly what we hear is contractors are pushing back because it finishes differently and it has different characteristics. But no, I have not heard that. I mean, that could potentially be a very easy fix. You mentioned earlier, where would I not recommend it and where would I recommend it? But I gave a talk to an engineering firm in...
Madison, Wisconsin a few years back and after I gave them the talk they said, well we should use internal curing everywhere because it doesn't just address shrinkage, it increases compressive strength, you can make your pavements thinner. Imagine, you know, a hundred miles of road where you take a half an inch or an inch of pavement out. That accrues to great big benefits but you know, I answered it by saying what was the downside was you do have to make sure the aggregate's preconditioned or pre -soaked.
And that's a good question. I will want to pursue that with some of Arcos's gurus and other folks at 213. The thing is, though, this internal curing water that's in the lightwood aggregate does not come out immediately. And the water that's absorbed in the aggregate is not part of the mixed water. You don't have to consider it. It's not part of your water -submit ratio.
Seth (30:51.419)
Right.
Seth (30:58.011)
huh. I would have thought the opposite. Like you got to do some, you got to do some math there to, cause that don't they do that with sand? Like if, if you get, if you bring surface water. Okay. All right. So they don't count that. Yeah. So they don't, they don't consider the, yeah. Cause how would you do that? Would you, I guess you compare the pre -soak condition.
Kevin Cavanaugh (31:10.38)
That's surface water. That's surface water. Yeah. Yeah, there you do have to conserve.
Seth (31:27.931)
to the soaked condition of that to figure that out? I don't know. You said it doesn't count, so I don't even want to try to wrap my head around that. Yeah, I'd be curious to see if people are going to that because people are trying to. I recently talked to Mike Hernandez. He's the technical director at AESCC. And he's got a survey.
Kevin Cavanaugh (31:36.428)
Well, we...
Seth (31:53.499)
that they are putting out to all the concrete contractors out there to talk about the issues that they've had with Type 1L cement. But he's more wanting to know which mix designs out there that folks have been successful with to, I guess, tackle the challenge of Type 1 cement, since it acts differently than what we've been using the Type 1 to cement. So yeah, I'd be curious to know if.
You're seeing an increase in that use and folks are using that as a lightweight aggregate as a possible solution to the type 1L cement performance. You mentioned the pushback from concrete contractors on the lightweight concrete because of the finishing. What are they saying? I mean, is it more difficult to finish lightweight concrete or it's just different or?
Kevin Cavanaugh (32:51.02)
No, that comment was with the 1L cements. That's what we heard from the local ACI meeting. But I do know that some contractors do worry about finishing lightweight concrete. A lot of times they want to do no air for some reason, put a hard trowel on it. And you have to wait for the bleed water to come up. Sometimes it's a different timing than what they're used to seeing. So it's just a matter of having pre...
Seth (32:55.483)
okay.
Kevin Cavanaugh (33:19.084)
pre -poror conferences or pre -job meetings to iron out all these questions. And the lightwood aggregate industry has technical reps that are more than willing to sit down with the ready mix producer and the concrete contractor. And that was basically the thrust of my conversation at the ACI Central Ohio chapter where you connected or Edgar Bauer connected the two of us.
Seth (33:44.315)
Yeah. Yeah. And make sure you're paying attention to your mix designs when you're bidding a job and, and checking and making sure you're dealing with normal weight or lightweight concrete. Cause I, I'm sure there's guys that overlooked that. yeah. is there anything else we're getting, we're getting close to the end here. is there anything else you want to discuss today before, we, before we, in.
Kevin Cavanaugh (33:58.284)
Yeah.
Seth (34:13.499)
the show. Told you 30 minutes goes quick.
Kevin Cavanaugh (34:18.092)
It goes real quick. Yeah. Next time I'm going to organize my thoughts a little bit better so I have like, you know, when I do it. Yeah. But I, there's been a misnomer for years of lightweight concrete causes trouble with floor coverings. And it goes back to 20 years or so ago when the VOC adhesives were, you know, they were outlawed or disallowed, whatever.
Seth (34:24.091)
You did fine.
Kevin Cavanaugh (34:47.596)
the mechanism was, but a lot of thought came out, the lightweight aggregate is allowing moisture to seep through and it's causing a problem with the adhesives. And that turns out not to be accurate. I can send follow -up information to you, or maybe we could talk about that in the next installment of this, where I can have one of the other ARCOSA folks who's real expert in this and did the research. And I shared that information with the group at the...
ACI chapter meetings I've been in. I don't have the top of my head right now, but it was not the lightweight aggregate really that caused the problem. It makes sense that it would be because it's an absorptive aggregate, but the research found it was pretty much the same with either type of normal weight or lightweight aggregates. There's a lot of atmospheric concerns. Like today, it's...
Seth (35:40.587)
yeah, we've talked about that topic several times.
Kevin Cavanaugh (35:47.404)
Yeah, it's very humid up here today in Milwaukee, and a lot of has to do with the ambient conditions about how that deck cures initially before you put the, and whether the structures enclose, whether there's heating, any, all that stuff has an impact. So we fought that for a long, long time, and I think we finally got past it, but it's planted in this.
the minds of many engineers and practitioners that it's a challenge. Like the term lightweight. A lot of people think lightweight means not very strong, not durable.
And that's not necessarily true. This is a ceramic structural grade material and it's used in offshore oil structures in Arctic environments specifically to resist ice floes. It has better abrasion resistance. So there's some misnomers like in the concrete block world, there's lightweight, there's medium weight, normal weight. I would like to consider that the...
Heavy weight or the normal weight stuff is ordinary and the lightweight concrete, masonry units or lightweight concrete is extraordinary. It's all nomenclature and a lot of that nomenclature provides different connotations in people's minds.
Seth (37:08.667)
huh.
Seth (37:18.683)
Yeah. So yeah, lightweight means weight, like it's light to pick up versus light, light, not lightweight. Like it's weak. So still concrete.
Kevin Cavanaugh (37:24.908)
It is. Yeah.
Kevin Cavanaugh (37:32.62)
It's still concrete. Yeah.
Seth (37:34.491)
That's right. All right. Well, Kevin, yeah, no, I'd love to have you guys come back on the show. We can talk about lightweight concrete floors and as far as its interface with flooring, we've talked about that before. Definitely could get the lightweight concrete perspective on that. But yeah, it's not the concrete's fault, majority of the time. So we can decide.
We can discuss that in the future. Kevin, thank you for coming on the show. And folks, until next time, let's keep it concrete.
Kevin Cavanaugh (38:10.572)
Thank you.
Kevin currently chairs several industry committees including ACI/TMS Joint Committee 122 on Energy Efficiency of Concrete and Masonry Systems that is charged with developing national energy code standards, the Expanded Shale Clay and Slate’s (ESCSI) Masonry Committee and the Concrete and Masonry and Hardscape Association’s Masonry Technical Committee (CMHA). He has worked for large, multi-national and small, family-owned CMU manufacturing companies and several lightweight aggregate suppliers. He enjoys the people in the concrete and masonry industries and educating owners, engineers, and state DOTs on lightweight concrete… and lightweight aggregate’s… many benefits.
Kevin earned a BSME at the University of Maryland and interned at the National Institute of Standards and Technology, where he first became involved with the concrete and masonry industries. After graduation, Kevin accepted a position as NCMA’s Energy Engineer. Two years later, and to better understand what NCMA’s members faced in their markets, Kevin launched his career in technical sales, marketing and product development of lightweight aggregate, concrete masonry and associated concrete and masonry products and systems.
Kevin has lived in Milwaukee for the last 30 years, but grew up in the Washington, DC area and is long suffering Washington Redskin’s fan.
________________________________________